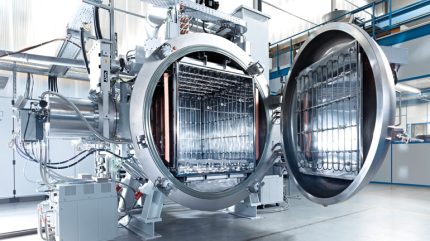
Heat treatment is a common procedure used across multiple industries, for example with the purpose of hardening metals. However, when heat is applied in a furnace, products may react with the oxygen in the air at an accelerated rate, causing changes to the metal’s properties and even damages to the equipment itself. This process is known as oxidation and can be avoided using vacuum.
“In a vacuum furnace, air is evacuated, meaning that the oxygen content is greatly reduced. This prevents the oxidation of materials at high temperatures, which is particularly important for materials sensitive to oxidation such as metals,” says Christian Burger, Market Manager for Thin Film Deposition & Metallurgy at Pfeiffer Vacuum.
The evacuation of air also comes with several other important advantages, adds Burger. In furnace processes run under vacuum, it is possible to avoid contamination and other unwanted chemical reactions, which is important when producing high-purity materials. This method is also used for degassing materials, with gases trapped in porous workpieces removed under vacuum to improve material quality.
According to Burger, the vacuum environment leads to more uniform and controlled heat transfer by eliminating the possibility for convection, since no air is present.
“This can help to reduce distortion of workpieces during heat treatment, which is particularly important when precise dimensions and shapes need to be maintained,” notes Burger.
He adds that the atmosphere can be further controlled by introducing various gases to enable specific chemical reactions or processes.
Applications for vacuum heat treatment
Overall, the use of vacuum in high-temperature applications enables more precise, controlled, and high-quality processing of materials, making it a critical process for various industries such as metallurgy, power tools, and electronics. One of the most common application areas is in aerospace manufacturing, which typically relies on reactive metals like titanium. High-vacuum brazing – a fabrication technique for joining metals – is also becoming more common in automotive and aerospace manufacturing.
Whatever the application, a tight furnace is one of the hallmarks of an effective vacuum furnace process. The process gases that are used during the treatment can cause sealants in the furnace to age at a faster rate than normal. In addition, over time, the vacuum process causes the metal vessel itself to wear thinner and thinner, with each furnace run wearing down some of the inside vessel. Eventually, this can cause leaks which could compromise the integrity of the workpiece.
“No furnace is hermetically tight, so the question is what leak rate do you allow?” says Burger. “There are general heat treatment processes that require only a light vacuum where the pressure is still relatively high, usually in the range of 1 mbar to 100 mbar. That’s not hard to achieve and it means you can allow a higher leak rate.
“For other processes like high-vacuum brazing, you might be looking at 10-5 mbar, which is relatively deep for a general industrial serial production process – and of course, when you have lower pressure, you can only allow smaller leak rates.”
The most important thing to avoid is the ingress of oxygen from outside the system, but it’s also vital to ensure there are no leaks within the system. Water cooling vessels are a common culprit, as they have the potential for water to leak into the furnace and damage the materials. This can even cause a large explosion as the water evaporates rapidly under the extreme temperatures, causing a very high overpressure due to the change in volume.
Leak detection methods for vacuum furnaces
A reliable leak detection regime is essential for identifying leaks and addressing them before they impact pump-down efficiency or product quality. It’s common to start with the pressure decay (or ‘leak-up’) test to determine whether a relevant leak is present or not. Following this method, the vessel is evacuated, tightly closed, and the differential pressure is evaluated after a period of time.
The leak-up test should always be performed after any maintenance or repairs have been carried out on the system. It’s also important to do regular checks outside of repair work, with the frequency of tests depending on how often the furnace is run and under which operating pressure.
When an unacceptable leak rate is registered via the pressure decay test, it’s time to detect the source via helium spraying or sniffing. During helium spraying, the furnace is pumped down to its operating vacuum level and a leak detector module like Pfeiffer Vacuum’s ASM 340 can be connected in front of the pump, between the pumps, or at the pump outlet. Outside the furnace, a spray gun is used to spray helium around all external flanges and seals, or any other connections where leaks may be likely to occur. If a leak is present, the helium will be forced inside the vessel and will eventually stream through the pump and into the leak detector.
According to Burger, helium spraying’s main limitation is the contamination of the leak detector with the range of gases present inside the furnace. This is often a big sticking point for OEMs.
“To avoid contaminating the leak detector, you would prefer to do it the other way around,” he explains. “If you have the chance to fill the furnace with helium or hydrogen, for example, you can do it vice versa using a sniffer probe instead of the helium spray gun.
“On the other hand, you are then testing in the wrong direction. It is always better to pick the method with a flow direction that is most similar to the actual situation, but this is not always possible because of the contamination issue.”
If there are any doubts as to the best method to use and how and when to conduct it, Burger recommends speaking to your OEM. “In the past ten years or so, companies in this industry have made their maintenance teams smaller and smaller, with more repairs carried out by OEMs,” he says. “In addition, you have a generation change underway where a lot of leak detection knowhow and experience is being lost. Sometimes you don’t use a leak detector for six weeks, so it’s hard to accumulate the experience. With the lack of leak detection knowhow that we see, more and more people in the industry are now struggling to maintain the quality they have had for years and years.”
Pfeiffer Vacuum has developed a wide portfolio of products for vacuum furnace operations, including ultra-high to rough vacuum pumps. With almost 60 years since the company introduced the first ever helium leak detector to the market (the ASM 4), Pfeiffer Vacuum has built a wealth of leak detection experience and knowledge specific to the vacuum furnace industry, making its team well-placed to provide technical advice on appropriate testing recipes and technologies.
To learn more about leak testing considerations for the vacuum heat treatment industry, please download the whitepaper below.