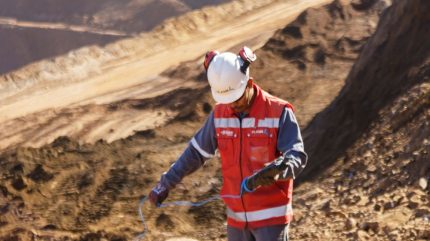
Mineral mining requires rock fragmentation, but conventional blasting processes often generate significant vibration, pollution, noise, and gas emissions. As protective environmental legislation ramps up, mines must adjust their operations to protect local communities, and the planet.
Alternative solutions need to be on offer that maintain operations while minimising environmental impact. A completely non-explosive product, Plasma4th is emerging as a viable solution to square this circle and improve the ESG credentials of many mines.
A solution to reduce noise, vibrations, and pollution
Key mining areas across South America and South Africa often struggle to reconcile the demands of their environment with the need for essential raw materials like copper, silver, gold, iron, zinc, and platinum, among others.
“There’s a very big mining area in Brazil, for example, but they also have to deal with a lot of environmental restrictions,” explains Javier Navarrete de la Barra, global business manager, Plasma4th at Enaex. “You’re not allowed to blast with explosives near this area, so they need other kinds of technology”.
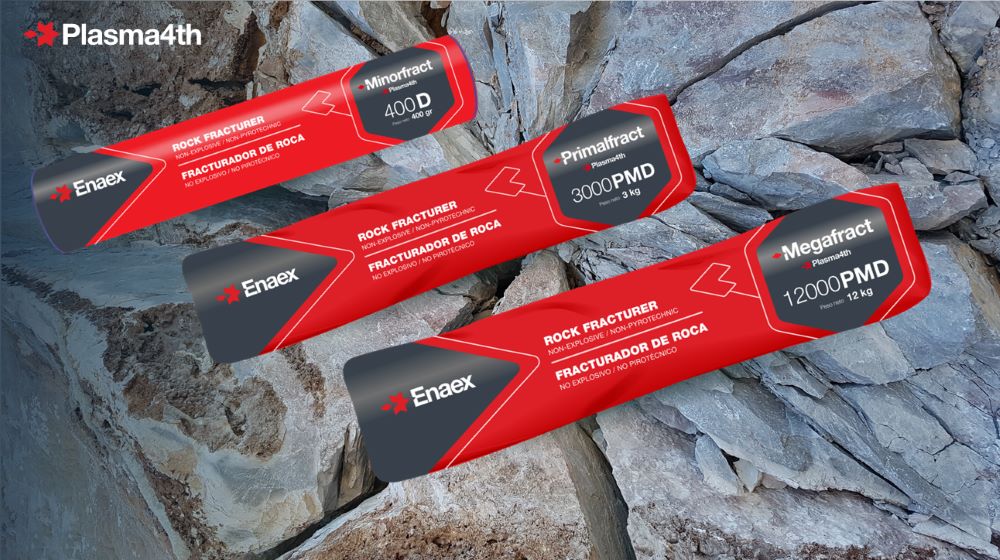
“In other cases, in Peru for example, they have problems with communities living very close to the mine, sometimes within 200 or 300 metres of it. They need solutions that produce less noise and fewer vibrations.”
To resolve this challenge, a Chile-based blasting services firm, Enaex, has developed the only 100% non-explosive product on the market, Plasma4th, a mixture of rapidly expanding metal salts. The salts initiate a thermochemical reaction triggered by a high-voltage spark in a confined space, thus generating significant amounts of thermal energy. The resulting gases then expand and fragment the rock.
“We don’t view rock fragmentation using Plasma4th as a replacement for conventional blasting, but as a complementary solution that adds value in situations where the use of explosives is either prohibited or intrusive,” adds Navarrete de la Barra.
Compares to explosives, Plasma4th converts only 5% of its weight into gases – none of them nitrous. Alongside other benefits including reduced noise, fly rock, and vibrations, using Plasma4th over other blasting methods drastically reduces the amount of pollutants released into the environment.
As well as being a more planet-friendly alternative, Plasma4th requires minimal evacuation zones that can have a radius as small as 100 metres for equipment and 150 metres for personal. For comparison, conventional explosives require a minimum distance of 500 metres.
Without compromising overall safety, these smaller zones translate into substantial cost savings, reducing equipment moving and facilitating continuous operations. Reduced exclusion zones also minimise stoppages in other critical areas, allowing crushers, stockpiles, concentrators, and offices to remain operational and improving the mine’s overall productivity.
Improve safety and maintaining efficiency with Plasma4th
Plasma4th has already been deployed at several mining locations across the globe, from Chile to South Africa. Projects include open-pit and underground mining to surface and underwater excavations in civil engineering.
One notable case study is at the Coimolache Mine in Peru, where material needed to be extracted just 200 metres away from a private residential area. The use of conventional explosives was unfeasible due to safety regulations, which required a 500-meter exclusion zone. With the use of Plasma4TH, the influence area was reduced to 150 meters initially and later to 100 meters, after confirming the total absence of flyrocks. This ensured the safety of the nearby house and allowed operational continuity in adjacent areas.
In Brazil, Enaex has partnered with an iron ore mine for over two years. This mine has been banned from using explosives on account of the residents living just a kilometre away. Part of the operations can be carried out with mechanical methods, but deploying the Plasma4th solution is necessary as a complement to improve extraction efficiency in areas with extremely hard rock while complying with strict environmental regulations.
Plasma applications will increase in line with environmental regulations
With more than four million cubic metres of rock fragmented, and nearly 100 projects completed across mining and civil works, Plasma4th has become an established, essential technology within the mining world.
“The technology will remain complementary to conventional methods, but Plasma4th is a good solution, bearing in mind that every year environmental concerns grow stronger, and countries create more regulatory policies,” notes Navarrete de la Barra.
To learn more about Plasma4th and Enaex’s mining solutions, download the free whitepaper below.