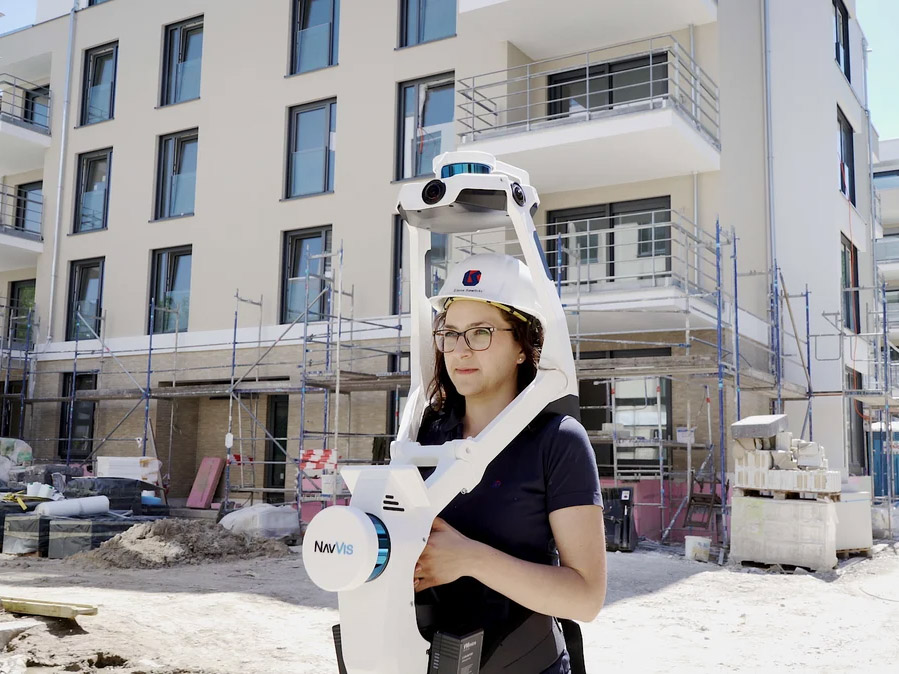
The construction industry can be slow to implement changes to established practices, notably regarding documentation. Documents are often not updated after construction ends even if there are subsequent changes to the building, with plans potentially lost in a filing cabinet for years and inaccessible to many stakeholders. Yet technology offers numerous advantages for documentation in construction, which negates many of the limitations of current methods.
At present, the majority of building documentation is in 2D form, compiled by professionals visiting sites and using cameras to take photos or measurements manually. In fact, many older buildings still rely on hand-drawn documentation. These traditional methods have serious constraints when it comes to compiling comprehensive building documents with many opportunities for gaps in information that can present considerable problems further down the line.
“Generally, the biggest problem is we are missing a lot of information by documenting construction sites or buildings with manual methods,” explains Baris Balota, solution manager for BIM/AEC at NavVis, a leading provider of mobile mapping systems and reality capture solutions. “Furthermore, planning experts who need to use these documents may understand them, but it can be a challenge for non-experts.”
Addressing issues with building documentation
Building documentation can also be susceptible to errors from the inaccurate alignment of datasets, wrong measurements, or general human mistakes.
But one of the core problems with building documentation is that it can be fragmented due to the different methods used separately by a range of contractors, which may not interact directly. For example, manual measurements are used to draw up 2D floorplans. While for more detailed 2D floorplans, total station instruments are used on-site.
More comprehensive means of 3D spatial measurement through laser scanning of sites can be time-consuming, expensive, and typically only be performed by trained professionals with experience in terrestrial laser scanning (TLS). Yet a TLS is a static device, meaning that objects or geometries may block areas from scanning, causing omissions in data and documentation.
Furthermore, long waiting lists are common for surveyors. Even when a surveyor is on-site, construction typically has to halt for them to conduct the survey to prolong already extended timelines.
Processing timelines present another delay. There can be long waits between when images and data are captured and when they are made available to partners and contractors. Consequently, there can be a lack of cohesion between datasets and collected materials, without a single source of truth, as well as issues with accessibility on different devices.
For documentation that is accessible, it is not always clear to understand for those without specialist training. Technological solutions can resolve almost all these issues, but a culture shift is required in the industry.
“In the construction industry, according to a study from McKinsey 2020, it took around 35 years to get to a BIM (Building Information Modeling) adoption rate of around 60%-70% in the US,” says Laura Rehlen, advanced solutions manager for AEC and BIM at NavVis. “Now in Europe, according to the European Construction Sector Observatory 2021, only around 30% of construction companies are using BIM – and that’s not a lot. Progress is slow. It seems to be one of the least digitalized sectors”.
The case for mobile mapping in construction
For building documentation, mobile laser scanning and simultaneous localization and mapping (SLAM) technologies have much to offer. Compared with TLS, mobile laser scanning and mapping can deliver substantially more in-depth capabilities in 3D data capture and reduce occlusions. Some devices are up to ten times faster at capturing on-site data compared with other scanning technologies.
“The advantage of mobile laser scanners is you can walk around objects and scan them from different angles and positions. Once complete, you have a more extensive point cloud,” adds Balota.
In addition, the combination of detailed 3D geometries and panoramic images not only increases understanding of the physical environment, but the addition of coordinates also pinpoints exact locations on a map. Any occlusions, or blind spots, can be averted with full visibility of a site.
With NavVis VLX mobile mapping system, comprehensive spatial data measurements are captured by two sensors, with one pointing horizontally and one pointing vertically, emitting approximately 1,280,000 points of light a second. While cameras capture 360° hi-res panoramic images for a complete visual representation of the data.
Scanned data and images are then uploaded to the cloud. Documentation can be available almost immediately in the online NavVis IVION platform, which can be accessed in a standard web browser, allowing users to move around a building virtually with similar functionality to Google Street View. A contractor will be able to view this point cloud data and panoramic images in advance of visiting a site to gather an in-depth understanding of the layout to allow for more effective planning and preparation for a physical visit.
“Sometimes, you may not be able to see very small details in the point cloud, but you also have the ability to check the panoramas to better understand the environment,” adds Balota.
Greater alignment between contractors and stakeholders
In some instances, there can be a lack of alignment between the designs of a building and the finished construction. Quickly identifying any deviations between the plan and the as-built is crucial to reducing rework time and cost, which is one of the biggest pain points in construction. Being able to compare plans with the physical building that is taking shape throughout construction also offers a substantial advantage in monitoring progress.
With NavVis VLX, scanning can take place at whatever intervals are required, offering the potential for far greater transparency and accountability in documentation during construction. For example, with regular scanning, it is possible to determine exactly what changes or works took place on precise dates on a project. Each scan represents the state of the construction from that time, and images and point cloud data can be shared easily with stakeholders.
The company’s hardware and software have been designed with interoperability in mind and are compatible with many of the latest versions of BIM and CAD tools. Through NavVis IVION, the reality capture data can be intuitively viewed and downloaded to then be used in third-party software tools for comparison purposes.
“Having access to up-to-date and accurate data allows you to make informed decisions about your project,” adds Rehlen. “You also have a high number of panoramic images, which increases transparency. While scanning, you can document everything and have the whole construction site as photo documentation accessible to view in 3D.
“We provide an easy-to-use and straightforward technology, both for the hardware and software. It’s no hassle to scan on-site. You can do it as often as you want to in different construction phases, as well as after you finish construction.”
To learn more about NavVis technology and how can help with your construction documentation requirements, download the document below.