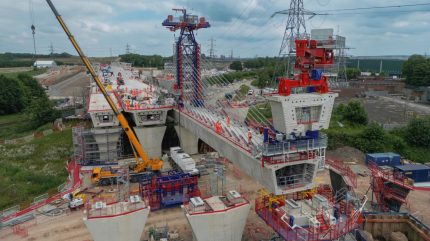
The construction of River Tame West Viaducts, part of the UK’s High Speed 2 (HS2) railway project, has reached a significant milestone with the implementation of a UK-first cantilever technique.
This new process was used to construct the first span of a 472m-long single-track viaduct in the West Midlands of England.
River Tame West Viaducts, comprising one single-track and one double-track structure, are integral to the Delta Junction’s design, enabling trains to traverse between London, Birmingham, and the north region of the country.
These precast segmental viaducts span the River Tame near Water Orton and connect to the Curdworth Box, which will carry trains over the existing Birmingham to Derby railway.
Construction of the viaducts’ 20 piers began last year, with the first spans completed in early 2024.
The process involved the use of two 42m truss beams to place segments, which were then moved by a skidding trolley and secured using post-tensioning techniques.
Following this phase, a 22m-high mast was erected to support the cantilever structure, featuring temporary post-tensioning cable stays and a 14m-high swivel crane.
This crane is responsible for installing the concrete segments one by one, completing each 45m span.
According to HS2, the permanent post-tensioning tendons are stressed to facilitate the removal of the temporary stays, leaving the permanent structure in place.
This process is repeated for each pier until all spans are finished.
The technique was originally developed by Campenon Bernard, now part of VINCI Construction.
BERD designed and manufactured the mast and swivel crane used in the construction.
A team of 40 is currently involved in the operation, with a total of 2,500 concrete segments to be installed using this specialist method.
All deck segments are expected to be in place by August 2026, and the same technique will be applied to build nine viaducts within the Delta Junction.
HS2 said that the concrete segments are produced at its outdoor factory near Lea Marston, where a 200-strong team recently celebrated the production of the 1,000th segment out of 2,742 planned for the six segmental viaducts of the Delta Junction.
Balfour Beatty VINCI’s Nicolas Gallone said: “This post-tensioning technology, pioneered by VINCI, is used on other major construction projects around the world. Now, it’s helping us to deliver these complex viaducts and overcome engineering challenges along the way, including existing waterways and utilities.”
Balfour Beatty VINCI, HS2’s main works contractor for the West Midlands, is overseeing the construction of 90km of the HS2 route, extending from Long Itchington in Warwickshire through Birmingham to Staffordshire.
The viaduct design is being executed by the Mott MacDonald and SYSTRA Design Joint Venture.