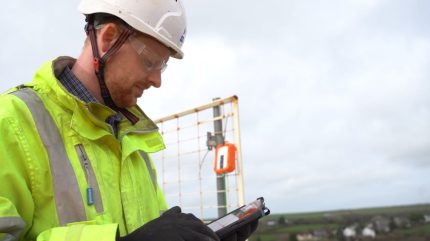
Infrastructure solutions company Costain has revealed that the adoption of Maturix’s concrete sensor technology has reduced the duration that a formwork has to be in place by an average of 33%, and resulted in time and efficiency savings for its customers.
The sensors, which monitor the strength and temperature of setting concrete, have been used by Costain’s materials engineers in various projects across the road, water, and rail sectors.
Maturix CEO Tobias Ejersbo said: “We are pleased that its engineers are seeing the benefits from using our real-time concrete monitoring system to keep track of the strength and temperature of dozens of pours across multiple different projects.”
The Gaia 200 sensors, which are noted to be comparable in size to a large smartphone, transmit real-time data on concrete temperature and strength directly to engineers and specialists.
This information is claimed to allow quicker, more informed decision-making, particularly regarding the optimal time to remove formwork after a concrete pour.
As a result, the duration of formwork placement is reported to have been reduced by an average of 33%.
Assessing concrete strength is noted to have traditionally involved physically extracting cube samples for laboratory analysis, with a typical pour necessitating around six cubes.
The direct and accurate readings from the sensors are claimed to negate the need for such tests.
On one Costain project, the technology was applied to more than 80 pours and structures, thereby avoiding the destructive testing of roughly 500 strike cubes.
Costain head of materials Bhavika Ramrakhyani said: “We’ve already seen enormous efficiency benefits. Programme delivery speeds have improved considerably, with striking times reduced by a third on sites where we have used the sensors.
“At the same time, the technology enables us to repurpose and reuse more of our temporary structures, as well as reducing the quantity of materials used, lowering our carbon footprint, which is another major benefit.”
Besides, to embed quality, predictability, safety, and low-carbon principles into their customer delivery teams, Costain has provided production thinking e-learning training to more than thousand employees.
Last month, Costain completed a pilot project to test the use of electric vans (EVs) across major construction project sites across the UK.