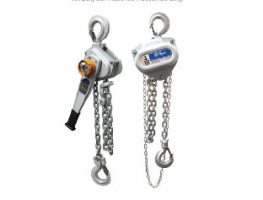
Brought to you by
Using a hoist underwater presents a range of challenges, from the physical issue of manoeuvring a lever while wearing thick gloves, through to the damage saline ocean water can do to equipment that isn’t properly prepared for the corrosive environment. Hoist manufacturers such as William Hackett and Ingersoll Rand have developed features that make their equipment more suitable for subsea lifting.
Tiger Lifting, based in Alnwick, Northumberland, UK, ensures its subsea lifting equipment meet the rigours of the marine environment through a research and development organisation the company commissioned in December 2015.
Called ORE Catapult, the independent, cross-disciplined organisation was tasked with carrying out a series of saltwater multiimmersion tests on Tiger Lifting’s subsea lifting hoists.
The tests determined how the hoists stood up to a pre-determined multiimmersion trial, which was specifically designed the replicate real-life subsea lifting scenarios. The successful results of the programme of tests were documented and now form part of the products’ technical files.
Using some of the knowledge gained through this testing regime, and the subsequent years of empirical evidence of the hoists being used in the field, Tiger Lifting developed and launched its SS19/20 range of hoists, which have been successfully internally verified for multi-immersion applications over a 54-day period.
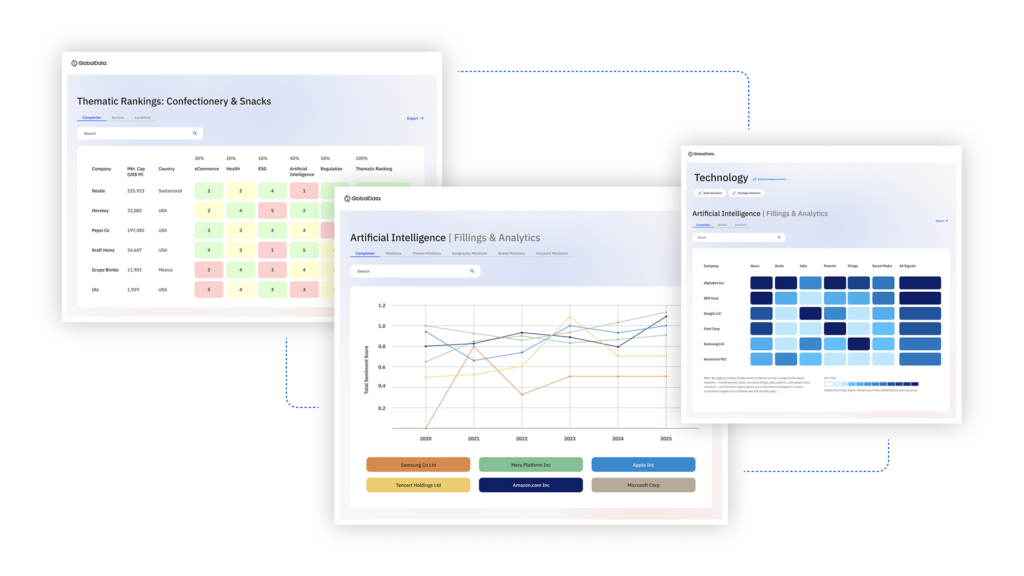
US Tariffs are shifting - will you react or anticipate?
Don’t let policy changes catch you off guard. Stay proactive with real-time data and expert analysis.
By GlobalDataFurther intensive internal testing guarantees that the hoists achieve more than 1,500 hours of protection to ASTM B117 conditions, the standard for salt spray/fog testing, ensuring that the performance of the SS ranges has been fully challenged in environments similar to the conditions they face in practical applications, says Tiger.
The SS19 and SS20 hoists offer a range of benefits, adds the company, including a two-stage finish designed to provide excellent corrosion protection and high impact protection suited for multiimmersion applications; the paint finish is in accordance with ISO12944 C5M.
The grease used is a high-performance new technology which can operate within a wide temperature range, and contains no heavy metals or other harmful or environmentally-unfriendly additives. It is formulated to the correct viscosity to prevent grease migrating from the area of application, and even when mixed with 50% high water absorption, the grease has excellent adhesion, and shows no sign of breakdown after 100,000 strokes and remains unchanged with no slump or breakdown.
Using the high-quality lubricant improves load carrying ability, mechanical stability, corrosion protection and water resistance, and increases operating temperature ranges; the standard operating temperature range of -40°C to 80°C far exceeds the requirements of current standards, says Tiger, and ultralow operating temperature units are also available to -60°C.
The company has also made improvements to various components within its products, including incorporating DU self-lubricating metal polymer bearings into its multi chain fall load sheaves. These have a unique composite bearing structure comprising a steel backing for mechanical strength and a porous sintered bronze interlayer impregnated with PTFE and lead for high wear resistance and very low friction properties, making them ideally suited to hoists used subsea, says Tiger. The low friction of the PTFE-enriched overlay provides improved energy efficiency, and the high wear resistance extends service life. The self-lubricating bearings also require no maintenance as self-lubricating bearings can operate perfectly when dry, but have greater reliability with lubricant to avoid potential shaft/bearing seizure under boundary conditions.
Recent enhancements to the brake system include bonded marine friction discs which are free from asbestos and are designed to provide an efficient and reliable braking surface for use in extreme conditions, and which are supplied with a grooved friction disc system that assist with dispersing salt water from between key surfaces, thereby eliminating failure through aquaplaning; precisely-engineered side plates and components protected by a full gasket to provide the brake chamber with maximum protection from external contamination; and an eight-point multi-start thread pinion shaft on the SS19 and SS20 hoists which doubles the lead distance, increasing brake efficiency by 100% over typical four-point threaded shafts, says Tiger. The company’s Quad Cam Pawl System guarantees permanent engagement of at least one of the two reciprocating cam pawls fitted to the SS19 hoist, ensuring full functionality of the brake in the event of a pawl spring failure.
Elsewhere on Tiger’s subsea hoists, forged latches incorporating a new wing design, making them easier to operate offshore or subsea; phosphor bronze bearings with tin to increase corrosion resistance and strength, and phosphorus to increase wear resistance and stiffness; recessed hook yoke forgings that offer full protection to the load chain anchor bolts on all bottom hooks, with precise tolerances preventing foreign objects from entering the load sheave area.
The SS19 also now features a redesigned pinion shaft and disc hub which adds more strength, and enables quicker and easier maintenance.
A better Hydraulic Hoist
Ingersoll Rand has made a range of improvements to its Sub Sea Hydraulic Hoist, designed for tough and unusual applications both above the deck and underwater.
These include a new hydraulic motor for high back pressure operation; the motor is smaller and more compact, says the company, and fittings are now internal for easier hoist handling. A new hydraulic brake, also for high back pressure operation, helps to enable the hoist to operate in higher-pressure applications.
Quick disconnects on both the main hydraulic supply and the return connections, and quick disconnects on all pendant hydraulic connects, assist the operator with easily connecting the supply and return line underwater, without using a wrench.
And stainless steel is used throughout the hoist to improve protection from the subsea environment: a protective stainless steel guard protects the quick disconnects while in storage, to optimise corrosion resistance and to prevent the connections from breaking while in storage or transit; stainless steel components prevent rust in salt-water applications; and a custom stainless steel pendant with extra-wide paddle buttons, suitable for divers’ gloves, increases ease of use underwater.
The Sub Sea Hoist is available with either a high-performance pneumatic or hydraulic motor. Both options have a fullysealed gearbox to enable safe, continuous operation at depths up to 70m underwater.
Developing standards
It can be a challenge developing a product that meets existing industry standards and recommendations; it adds a further element of complexity to the process when the product is designed to meet standards that haven’t been established yet.
This was the challenge facing UK-based William Hackett Lifting Products when the company looked into developing a lever hoist suitable for multiple immersions underwater. Existing recommendation from the International Marine Contractors Association (IMCA) specified no more than one immersion for any subsea hoist, explains Tim Burgess, owner and managing director at William Hackett. It fell to the company, therefore, to not only develop the product suitable for multiple immersions but to also develop a test regime thorough enough to appease the certification society DNV GL. Of course, salty water is not the only potentially hazardous substance below the surface of the ocean, the sea bed is formed of particulate which is easily disturbed by hoists and their loads, which can then damage the interior and exterior of the hoist, and the testing process had to reflect this. The SSL5 lever hoists were therefore tested in test tank environments containing agitated sand and oily sludge, explains Burgess, to accurately simulate the conditions that could lead to malfunction, wear or failure. The testing process also stipulated and recorded different storage and maintenance regimes between immersions varying from best practice to complete neglect. All hoists successfully completed the test regime and that was sufficient for DNV GL, who, based on William Hackett’s test regime, certified that the SSL5 lever hoist is suitable for multiple immersions over a 30-day period.
The company then commissioned field trials, during which the SSL5 hoists were immersed multiple times over a 60-day period, with the hoists successfully passing the multi-immersion test, inspection and operation programme previously witnessed and verified by DNV GL.
Multiple immersions from one hoist provides environmental and economic benefits, including a reduction in capital spend on new hoists per mobilisation.
“We are helping operators to make better choices and overcome purchasing large quantities of single-use hoists,” said William Hackett director Ben Burgess, talking at the launch of the SSL5. “The historic paradigm of single-use hoists, which are often used once and then discarded, is very expensive and not good practice from an environmental perspective. The use of single immersion hoists isn’t sustainable for today’s industry and is representative of an out-dated practice. Customer decisionmaking criteria is beginning to reflect this.”
Modifications were made to the hoist to make it more suitable for the rigours of subsea use, including the choice of material coatings, a marine-spec grease, stainless steel components such as springs and nuts—and precision-made side covers to replace the previous design which featured holes, to minimise ingress of contaminants.
Health and safety
The William Hackett SSL5 is now used around the World but continual investment in the design of the SSL5 has led to the development and inclusion of quad pawl technology. The new patented design, uses four pawls, doubling the number of pawls typically built into a lever hoist. This design guards against individual pawls or springs failing and—as the company has seen from its database of orders—the spare parts most commonly ordered are pawls and springs, highlighting the tendency of those components to wear in existing hoists. The offsetting of the pawls prevents them from being simultaneously disengaged, and allows for finer adjustments to the hoist. This development of the William Hackett hoist is called the SSL5 QP.
While this development improves safety during use of the hoist, another aspect of health and safety has also been addressed. The company spoke with the health and safety team at oil giant Shell, who said that 80% of accidents happen during the deployment of hoists—that is, moving the equipment into position ahead of lifting. A key challenge for William Hackett, therefore, was to reduce the weight of its hoist range. This was achieved with the SSL5, resulting in an improved performance-to-weight ratio achieved compared to typical earlier generation hoists. Further work has been done in partnership with the mechanical engineering department at Newcastle University to reduce the unit weight of adjustable beam trolleys explains Tim Burgess.
William Hackett is continuing to develop technical knowledge in product design and material properties leading to benefits in the oil and gas sector, particularly in the North East of England.
Lifting tools Assist Offshore
First Subsea has been awarded a contract to supply three Ballgrab Internal Lifting Tools (ILT) to Allseas, for use in offshore decommissioning projects.
The tools are designed to be inserted into a tubular receptable attached to the structure to be lifted. The specific ILT tools supplied to Allseas can lift loads up to 900t, and cover an internal receptacle diameter from 660mm–1,524mm.
Allseas’s first planned offshore operation with the ILT tools will be the Tyra Redevelopment Project, where the tools will be used to lift the top jacket structures for Tyra East D Flare Jacket and Tyra West D Flare Jacket.
First Susbea Ballgrab connectors have been used in offshore deployment and recovery operations since 1994, and have established a track record in both the oil and gas and renewable energy sectors, including decommissioning Frigg on the Norwegian continental shelf in 2006.
A more recent project involved the use of 600t-capacity ILT on the Wikinger offshore wind farm to lift a piling template from the deck of a vessel to the seabed then, after the piles were run, picking up and recovering the template. Over a period of three months the tool performed more than 150 lifting operations.
Environmental Subsea lubricant launched
Lubricant manufacturer Metalube has introduced a new wire rope build lubricant that is fully biodegradable and non-toxic to aquatic organisms.
Called Rope-Tek PBL3700 ECO, the lubricant was developed specifically as a build lubricant for wire ropes and is Ecolabel certified, fully Vessel General Permit (VGP) compliant, and is designed to work in conjunction with the Rope-Tek range of lubricants for steel wire ropes and umbilical cables operating in marine environments.
Douglas Hunt, commercial director at Metalube, said: “At Metalube we have always been committed to sustainability and the environmental impact of our products. This high-performance lubricant is specifically formulated from a combination of biobased, renewable materials complimented with performance additives that are proven to be non-toxic to aquatic organisms.
Protecting our oceans is now more important than ever and this latest ECO lubricant is certified to the EU Eco-label scheme and is therefore fully compliant with the USA EPA Vessel General Permit (VGP).”
The product is designed for application during manufacture of the wire rope, with the equipment used for standard hot melt compounds. It can applied at temperatures as low as 50°C, but has an operating temperature range of up to 110°C. It has an excellent resistance to moisture, says Metalube, protects against corrosion-induced failure, and provides high inherent lubricity which minimises wear of wires and strands.