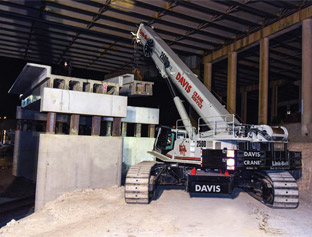
Brought to you by
“Time is money,” says Daichi Wada of Tadano’s marketing department. “This well-known proverb also applies to the crane business.”
Which is why operator assistance devices are part and parcel of modern crane usage. Recent years have seen a big evolution. Earlier days saw the likes of LMIs (Load Moment Indicators) and RCLs (Rated Capacity Limiters) help crane operators, but with advanced innovations and developments, today’s systems are much more sophisticated. Offering greater capabilities, modern crane operator assistance devices help boost safety and efficiency levels.
An example of developing crane operator assistance devices is the proven Tadano Demag IC-1 (Intelligent Controls) control system with integrated RCL (Rated Capacity Limiter).
Since its introduction in 2001, offering smooth crane operations, touchscreen operation with intuitive user guidance and advanced diagnostic capabilities, this control system has been constantly updated and improved.
“A major improvement was the introduction of IC-1 Plus in 2016,” says Wada. “This enhancement provides additional value to the crane as it increases flexibility and enables it to perform more jobs. The crane capacities are determined, depending on the slewing angle of the superstructure, counterweight and outrigger setting. Outrigger settings and counterweight configuration are detected in the IC-1 Plus.”
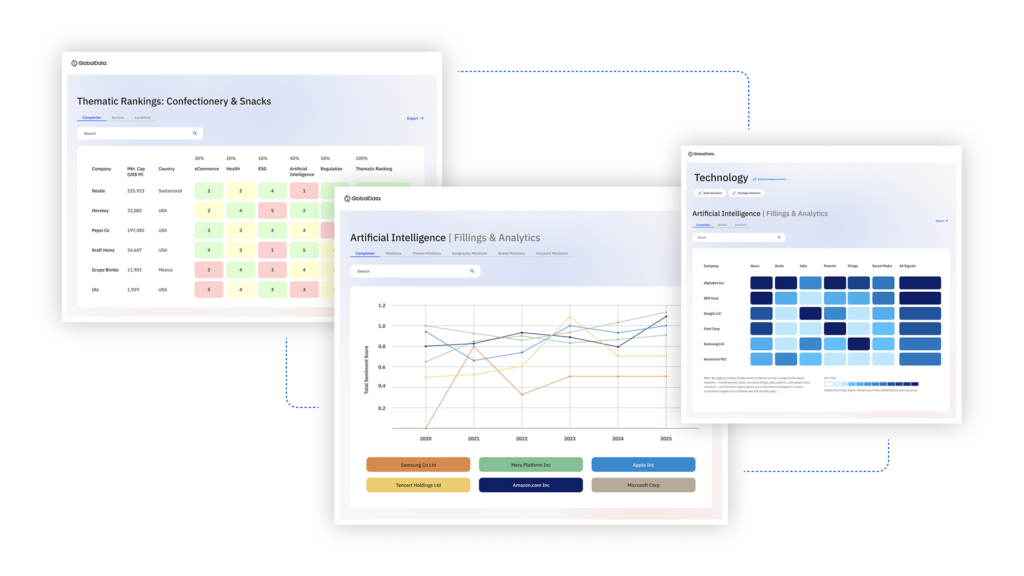
US Tariffs are shifting - will you react or anticipate?
Don’t let policy changes catch you off guard. Stay proactive with real-time data and expert analysis.
By GlobalDataThis year has seen a major update for IC-1, with the introduction of IC-1 Remote, a telematics system that provides advanced data for fleet management and bi-directional communication between crane and factory.
Wada explains that IC-1 offers superior handling of the crane due to an advanced human-machine interface with intuitive, easy to use operation. Customers can use their maximum lifting capacity, as the IC-1 Plus determines lifting capacities for every position of the boom, subject to the slewing angle of the superstructure.
“This enables them to use their maximum lifting capacity especially when lifting over the outriggers,” says Wada. “Plus, the (asymmetric) outrigger set-up allows the crane to work in confined spaces optimising lifting capacity under the constraints given.”
On the US-manufactured telecrawler side of the Tadano business, the Tadano Mantis GTC-Series telescopic boom crawler cranes with Opti-Width are capable of limitless combinations of symmetrical and asymmetrical track width set-ups. “No pinning of the track frames in fixed width positions is required, so it is ideal for the crane user to be able to position the track width optimally for their lift work and to have the proper load charts automatically selected by the AML-C system,” explains Julie Fuller, VP engineering, marketing, and purchasing, Tadano Mantis.
Fuller says that Opti-Width load charts for asymmetrically positioned tracks have significant lifting capacity enhancements when compared to those for symmetrical tracks: “A comparison of the mid-extension track width of the Tadano Mantis GTC-800 with a symmetrical mid-mid track position vs. an asymmetrical min-max track position [at the same operating width] shows capacities up to 67% higher over the max extension track side when compared to the symmetrical over side capacity.
“Opti-Width incorporates zoned load charts, rotational position sensing, and function soft stops to ensure that the crane operator cannot swing with a load into a zone where the crane will be out of capacity, or where backwards stability is limited.”
The simple functionality of the latest AML-F crane control system is also the basis for the low error-proneness of Tadano Faun all-terrain cranes.
“The crane control AML, with the latest version F offers the crane operator a clear and reliable system, which is very mature,” says Wada. “Thanks to this given infrastructure, the AML-F crane control system shows its strengths in the new models of the ATF series and is designed for safe and efficient crane operation with its multifunction display and rotary push-button.”
Wada explains that one of the most important functions is the Lift and Release Adjuster, which allows the crane operator to pick up and place a load without swinging. The asymmetrical outrigger base is also a tool that allows the crane driver to perform particularly well. “The core values of Tadano are safety, quality and efficiency. All components, including the crane control system, are constantly being improved from this point of view.”
The Tadano AML-F crane control system (which complies with EN 13849, the European norm for safety functions of control systems) determines, among other things, that the crane has redundant sensor technology, contains software that checks each other and has a secure data memory available that always displays the correct lifting capacity charts.
Tadano cranes also have a 3D work area limitation with the AML-F system. This allows the crane operator to limit the working range of all crane movements, resulting in no collision damage on non-transparent construction sites and automatic shutdown at the load limits.
Tadano Japan has developed three notable operator assistance devices. The HELLO-NET system allows a crane operator to check on day-to-day operational status, mileage and remaining fuel for each machine equipped with a communication terminal.
The newly developed Smart Chart brings out better crane performance, also while the outriggers are fully extended. “The Smart Chart expands the working area shape from a circular cone to a square pyramid, allowing you to get the best crane performance in any outrigger extension setup,” says Wada. “This feature is currently available for the GR- 1200XL/GR-1100EX and some rough terrain cranes and the new truck crane series.”
Meanwhile, the Tadano View System (available for the GR- 200EX Australian market only) has been boosted by two new functions: Wide Sight View (which increases visibility for an operator around a machine with a birds-eye view image shown on the large multi-function display) and Human Alert System (based on the left hand side of the crane and alerting the driver of people presence via a buzzer).
April 2019 saw the return of Bauma, the Munich-based trade fair for construction and building material machines, mining machines and construction vehicles and equipment. Here, Tadano showcased two new technologies.
“Lift Visualiser uses images from a load monitoring camera, enabling the driver to watch a load in the distance or in a blind spot from directly above,” says Wada.
“The screen also displays the performance range of the crane in real time. It gives an instant check on the critical area, ensuring safe and reliable crane operation.”
Lift Compass is a new type of radio remote controller that allows the operator to leave the cabin and operate the crane near the load while keeping an eye on it. “It is an innovative radio control system that allows the load to be moved in the same direction in which the operating lever is moved, once the positioning of the operator and crane have been input. It allows the crane to be operated intuitively and freely, without worrying about individual operations, such as turning and lifting or lowering.”
Also at Bauma 2019, Link- Belt debuted its new one-person fly erection technology on the 120USt (110t) 120|RT and 100USt 100|RT. Brian Smoot, all-terrain and hydraulic truck crane product manager at Link-Belt Cranes, explains that both the 120|RT and 100|RT have an available two-piece [35-58ft (10.7–17.7m)] on-board off-settable fly for greater flexibility and range, which manually offsets at 0, 15, 30 and 45°.
“Simplified one-person fly erection technology minimises work at height with ground level controls for fly assist and boom hoist cylinders,” says Smoot.
“Given the natural elevation of a rough terrain crane boom, one control raises and lowers boom angle from 0 to -3°, and another control is used for the fly assist cylinder. Boom head speed screws and numbered spring-loaded latches provide intuitive assembly.”
At the core of Link-Belt’s safety devices is the crane operating system Pulse 2.0. The most visible difference in the new 2.0 version is the 10in display, which is 47% larger than the original Pulse screen. “This has been carefully selected to deliver a high resolution screen which is tough enough for harsh operating environments,” says Smoot. “The Pulse 2.0 touch screen can be used with gloves and be seen in direct sunlight with larger, clearer images; and the unit is pivot-mounted for optimal viewing. The interface is more dynamic throughout the operating system with interactive indicator lights displayed on the margins.”
Once in the seat of the cab, operator start-up is quick and easy with a faster hardware/software response and fewer required operator inputs. Electronic level/ list display, as well as ground bearing calculator, is integrated.
Another advantage of Pulse 2.0 is its accessibility. “Operators who may have felt overwhelmed in the past by other crane operating systems will find the 2.0 system to be the system of choice going forward,” comments Smoot. “One specific feature added, based on operator input, is the ability to shut off the engine and still maintain live display data for an extended period of time.”
Pulse 2.0 is designed to be user-friendly with a simple pictorial design. For a safer experience, Smoot says that the system has the ability to make imaginary walls and planes for restrictive picks that alert an operator when approaching or entering a restricted zone. As well as this, diagnostic information and fuel levels can be reviewed on iCraneTrax for a site supervisor to help anticipate and schedule regular and routine maintenance, eliminating last minute surprises.
“One of the most exciting enhancements with Link-Belt Pulse 2.0 is the ability to service and update a crane’s software remotely,” says Smoot. “The system includes a Wi-Fi hub and uses the serial number of the unit to determine whether any updates are available, and downloads/ installs to the appropriate controller. Software maintenance can be accomplished in the field without a service call or bringing the crane in for service.”
Liebherr offers several technologies which assist the crane operators. One of the most notable examples is the VarioBase system which enables each individual crane support to be extended to an arbitrary length. “The load moment limiter within the LICCON control ensures that the crane can operate safely,” explains Wolfgang Beringer, marketing and communication, Liebherr-Werk Ehingen. “This prevents accidents by human error during both the set-up and when hoisting loads.
The system calculates the precise lifting capacity for any support base and thus monitors the crane’s stability.”
Liebherr has developed various measuring and calculation technologies for this purpose. These include a length measurement system that records the precise extension position of each support strut; and a sensor which establishes the exact support force. This technology enables the crane control to calculate the maximum lifting capacity for the superstructure at every angle position. A monitor for the driver shows all the relevant parameters.
VarioBase also increases efficiency for crane operations by ensuring higher lifting capacities.
“The system identifies the machine’s precise centre of gravity and the tipping edges and then sets the two relative to each other,” says Beringer. “If a load is hoisted over a support, the risk of tipping is lower than during hoists to one side, for example. This means that the system can permit a higher lifting capacity and loads can be moved to a greater outreach.
“These benefits also apply when the supports are extended to their maximum length. The greatest increases are in working ranges above the supports when partial ballast is also in use. The increases in lifting capacities mean that ballast transport is simply not required for many crane jobs.”
VarioBase has proven popular with a broad spread of clients such as Hull-based Central Crane Hire, which used the system for its new LTM 1200-5.1. This will result in higher lifting capacities and bigger working range.
VarioBase was essential for work undertaken on the dismantling of a construction crane in the Bavarian town of Landshut earlier this year. The job was performed with the aid of a Liebherr LTM 1250-5.1 mobile crane, which was set up in a narrow 8.5m wide alley.
With the narrow width of the area a potential problem, VarioBase overcame this issue with its variable support program that allowed each of the supports to be positioned individually, with enough room free to allow for passers-by—the supports were extended to roughly 75% on the side facing away from the load.
Narrow space is a common obstacle in construction, which was the case for a job concerning the replacement of an old railway bridge in Aarwangen, Switzerland.
The bridge in question was only seven metres in width, but VarioBase again saved the day with its support system that allowed the arbitrary length extension of each crane support.
Modern operator assistance technology also extends to smartphones via specially tailored apps. Manitowoc is one such company to take advantage of apps which are perfect for instant, on-the-go crane work. One of these is a free boom configurator app that allows operators to quickly determine the set-up of the crane. Using the smartphone app, assessing the complete boom and job length combination for lifting is a fast and simple task.
With the aid of a sliding scale, the user can choose precise boom and jib length combinations, building heights, boom radii and other crane parameters. John Alexander, director of all terrain crane service, mobile training, and telematics at Manitowoc, explains: “By simply entering a few details, the app immediately generates a setup for that specific lift. It is a great tool to use during pre-planning or on site to get the job done.”
Another of Manitowoc’s free apps allows users to diagnose any technical problems that may arise on cranes. Crane operators can use the app to interpret diagnostic codes which are generated by on-board control systems. The app immediately tells operators and owners the meaning of the codes, allowing quicker repair work and eliminating the need for third-party intervention. Alexander cited this app as an example of the “new era of crane operation” which can “harness the power of mobile devices”, adding: “By accessing a cloud database right from their smartphones, companies can quickly get valuable diagnostic information to keep their cranes up and running.”
As well as diagnostic codes for Grove and Manitowoc branded cranes that run on Manitowoc’s Crane Control System (CCS) and GMK cranes with ECOS1 and ECOS2 systems, the app was recently updated to now offer diagnostic codes for National Crane models NBT30H-2, NBT50, NBT55, NTC55 and NBT60 and for selected Grove and National Crane Rated Capacity Limiter Systems.
The apps are available to download for free at both the Apple app store and at Google Play for Android devices.
The future is all about benefiting crane operators further. With bigger and better ideas developing all the time, the emphasis, as Wolfgang Beringer comments, is on “more assistance to make it easier to operate a crane.
“Telemetry is also an important development in order to assist the crane operator from the side of operating company as well as from the side of the manufacturer.”
“As wireless technology evolves, additional functional aspects of lifting can be done remotely,” adds Smoot. “Currently, Link-Belt offers an optional wireless remote control system for the TCC-1200 and TCC-1400. The wireless remote provides a solution for industries and other operations where environment may require it, allowing the operator to be out of the cab and still have control of the crane.”
According to Andreas Hofmann, head of R&D at Tadano, the following topic will play an important role in the future: “This will be the beginning of autonomous crane operation, which will autonomously monitor the crane from a kind of control point. This allows conclusions to be drawn about both safety and efficiency.
“The Machine-2-Machine communication will be a new milestone in crane control.”