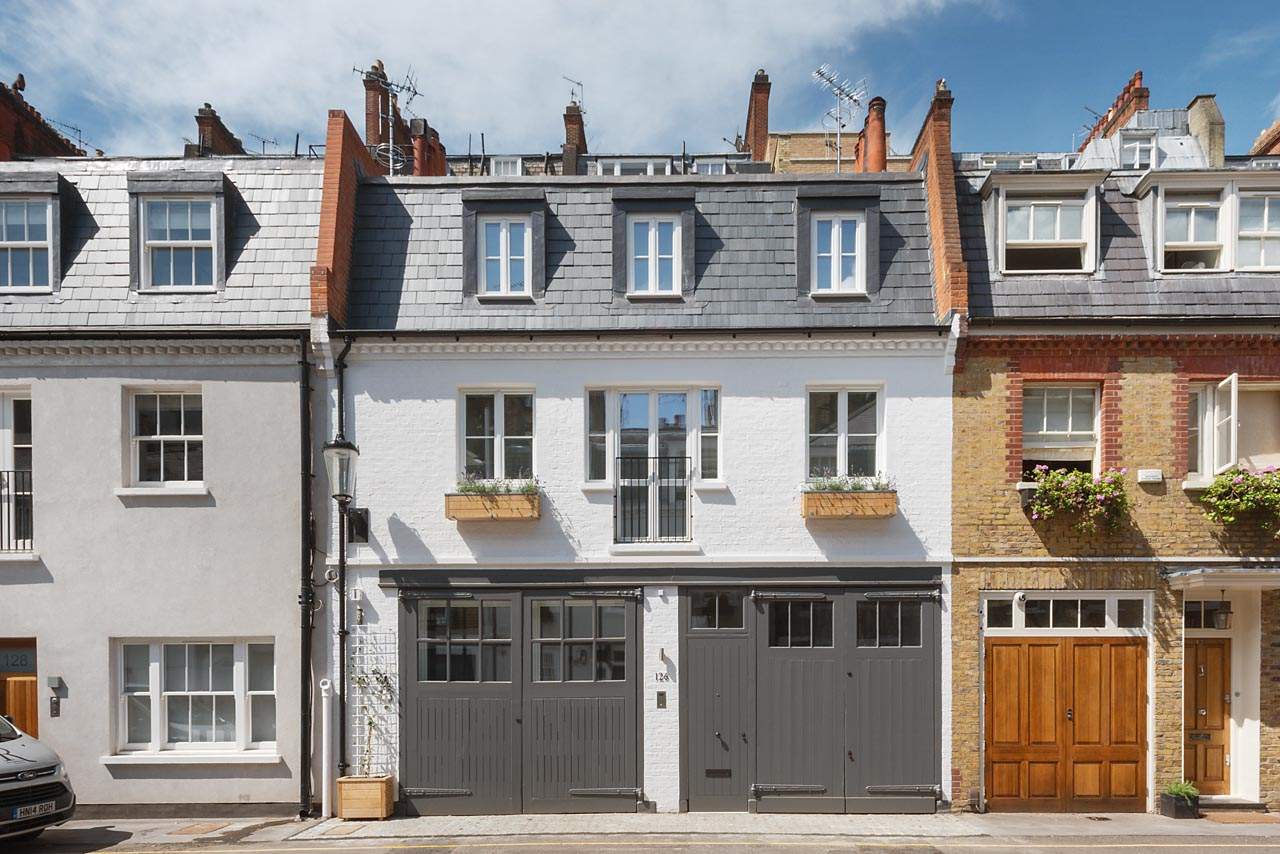
Nestled halfway between Sloane Square and Knightsbridge tube stations, a 19th century period mews house has become one of the only period properties in the UK to become a PassivHaus-classified building.
Retro-fitted by Cadogan Estates over a three-year period, it has also achieved an outstanding BREEAM rating (sustainability assessment method). The result is a luxurious, historic property that will reduce energy bills for tenants by 85%.
“We wanted 126 Pavilion Road to set a new precedent in environmental performance, by meeting the demand for an energy-efficient property in a highly desirable location,” says Hugh Seaborn, CEO of Cadogan.
“From the outside, the PassivHaus looks no different to its neighbours, retaining the heritage of the area, whilst internally it has been tastefully refurbished and retrofitted with cutting-edge energy efficient measures.”
What is a PassivHaus?
The PassivHaus concept was developed by Bo Adamson of Lund University, Sweden, and Wolfgang Feist, director of the Passive House Institute in Germany, about 25 years ago. Climate change, fuel poverty and the need to reduce dependency on fossil fuel use in Europe were driving forces behind the goal of achieving a performance standard that fitted with architectural tradition and the construction of environmentally-friendly, energy-efficient buildings.
Now there are more than 30,000 PassivHaus properties worldwide, including commercial and industrial buildings, as well as residential homes. In a PassivHaus, no traditional heating systems are needed, and extensive criteria must be fulfilled for a property to achieve PassivHaus status.
The “Space Heating Energy Demand” in a PassivHaus must not exceed 15kWh per square metre of net living space per year, which means that annual fuel costs are reduced by a factor of 5-10. PassivHaus estimates that “a household living in a 70m2 Passivhaus with gas heating could spend as little as £25 on space heating each year”.
There must also be efficient heat recovery ventilation (where at least 75% of the heat from exhaust air is transferred to the fresh air again by means of a heat exchanger); airtightness (according to a limit for uncontrolled leakage through gaps) and the avoidance of thermal bridges.
The challenges
A PassivHaus requires specific, certified windows and with 126 Pavilion Road being a period property in the heart of the Hans Town Conservation Area (which contains many buildings that are listed for their special architectural or historical interest), this was one of the most problematic areas.
“The biggest challenge was establishing the design of the replacement windows,” explains Andrew Gilbert, director RIBA at Latitude Architects. “One of the planning requirements was to use traditional timber sash windows to match the corresponding properties in the conservation area, but PassivHaus properties cannot obtain certified sash windows,” he continues. “In the end we agreed with the planners to use casement windows as a solution before resubmitting our material amendments within our application.”
The existing single-glazed windows and roof lights were eventually replaced with triple-glazed timber PassivHaus-certified units. “Being PassivHaus certified they have already been tested to a high level of airtightness, which is critical for a PassivHaus property,” he says, adding that the airspace provides a far greater thermal performance.
Overall the indoor air quality of PassivHaus developments is considered to be outstanding. It is achieved by the airtight seal on the property which reduces the air infiltration rates and the MVHR unit which filters and post heats fresh air.
Another challenge was to ensure the airtight seal of the building was greatly enhanced compared to standard Building Regulations.
“Any cold bridges through the external fabric were omitted,” says Gilbert. “Any proprietary elements installed in the external facades, including windows, doors, roof lights and vents, had to be PassivHaus certified to ensure the criteria was met.”
High performance insulation, a product called “Spacetherm Aeorgel” (which is derived from silica gel) was also used. “Half the thickness of a standard PIR insulation, it also allows thinner wall build ups, which is particularly useful around tight details such as Dormer windows,” he says.
While the use of mineral wool and rigid PIR insulation to the walls, floors and roofs are not that different from standard detailing of non-PassivHaus buildings, Gilbert explains that additional complexity comes into play when creating higher levels of airtightness, while simultaneously avoiding any cold bridges.
“Most thickness of insulation were increased and in specific areas, such as the dormer windows, high performance aerogel was introduced to address this,” he says. “The roof insulation was also raised above the roof to ensure the entire structure remained warm, which in turn increased the roof height slightly.”
Preparation and planning
Gilbert explains that during the initial planning stages, the building was not treated as a PassivHaus property, which meant the details for the PassivHaus submission – to ensure they compiled with best practice – were developed with Sturgis Carbon Profiling, a consultancy firm dedicated to supporting a sustainable, low carbon built environment.
Before the work went ahead, prepping the contractors played a crucial role in ensuring that the PassivHaus retrofit would proceed correctly.
“The education of contractors was very important, to make sure they understood the process and implications if should they fail to do the work correctly,” says Gilbert, adding that demonstrations were set up with the tape manufacturer on site to show how all the specific tapes should be used on the various functions.
“Programming the works was very important to ensure each element was completed before the next phase was progressed,” he continues. “If the end of the construction had been reached and the airtightness was not reaching the correct levels, it would have been very difficult to locate the problem.”
To ensure the quality was maintained throughout they nominated one individual on the contractor’s team who was responsible for airtightness.
The finishing touches
Seaborn says that one of the battles faced with 126 Pavilion Road is challenging the perception that environmentally-friendly and energy-efficient properties are unable to be as luxurious as those which are not restricted in terms of materials and fittings.
“We paid close attention to ensure all of the finishes and fittings are of the highest quality,” he says, “from the beautiful engineered oak floor to Domus tiling, and matt bronze Strada London ironmongery.”
But even if this prime property is luxurious enough to justify its rental price tag of £1,795 a week, the performance of the property and its smart energy metres will be the test as to whether Cadogan enters into further retrofitting activities.
“Once we have the results we can decide whether to roll out these measures more widely within our residential portfolio,” says Seaborn. “This will include looking at energy efficiency and wellbeing benefits for its residents.”