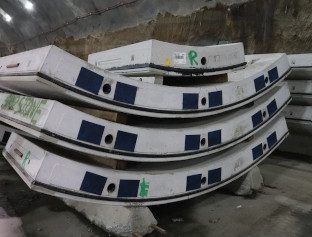
Brought to you by
The use of fibre reinforced concrete (FRC) for the production of precast segments in tunnels linings mechanically excavated through tunnel boring machines (TBMs) is one of the most promising application of this material, reducing or eliminating the traditional steel reinforcement. The use of steel fibres as a main reinforcement has been continuously increasing also due to the definition of guidelines for the design of FRC. A reference document for designers, clients and construction companies is the Model Code 2010, presented by the International Federation for Structural Concrete – Fédération international du béton (FIB) in 2013, containing a specific part related to FRC. In this framework, FIB Commission 1 Concrete Structures introduced a series of documents related to the use of structural concrete in underground construction and the FIB Task Group 1.4 “Tunnels” decided to create a Working Party 1.4.1 on “Tunnels in Fibre- Reinforced Concrete”. The result of the work made done for fib WP 1.4.1 is the Bulletin 83 “Precast tunnel segments in fibre-reinforced concrete”, prepared to support all stakeholders in introducing FRC in this type of applications.
Fires in tunnels present particular dangers and its occurrence has to be certainly prevented. A well-assessed procedure for evaluating the bearing capacity of FRC sections, without any traditional steel reinforcement, exposed to fire is still missing. A better understanding of concrete behaviour and structural mechanics is required in order to improve the design of FRC structures with respect to fire, to the advantage of engineers looking for better and safer design standards. A proper assessment of the structural behaviour under fire exposure is important either in design phases, for example for extending the service life of the structure, or in repair and strengthening of existing structures, such as in case of rehabilitation after an occurred damage. Furthermore, new techniques for the assessment of fire damage in concrete structures have made deriving residual properties of concrete much less uncertain than in the past.
1.Heat Transmission Equation
The heat transmission within an isotropic solid body, with internal heat generation, in unsteady conditions is governed by the Fourier’s equation. The main parameters defining the thermal problem are the thermal conductivity λ, the density ρ and the specific heat c of the material of the section.
In case of fire inside a tunnel lining, characterised by a one-dimensional heat transfer, with a null internal heat generation and a constant value of the thermal conductivity within the body, Fourier’s equation can be reduced to a simplified equation, in which only the second space derivative and the first time derivative of temperature compare. According to these hypotheses, the thermal parameters can be grouped in one quantity only, known as the thermal diffusivity ? and defined as the ratio between α and the product of ρ and c.
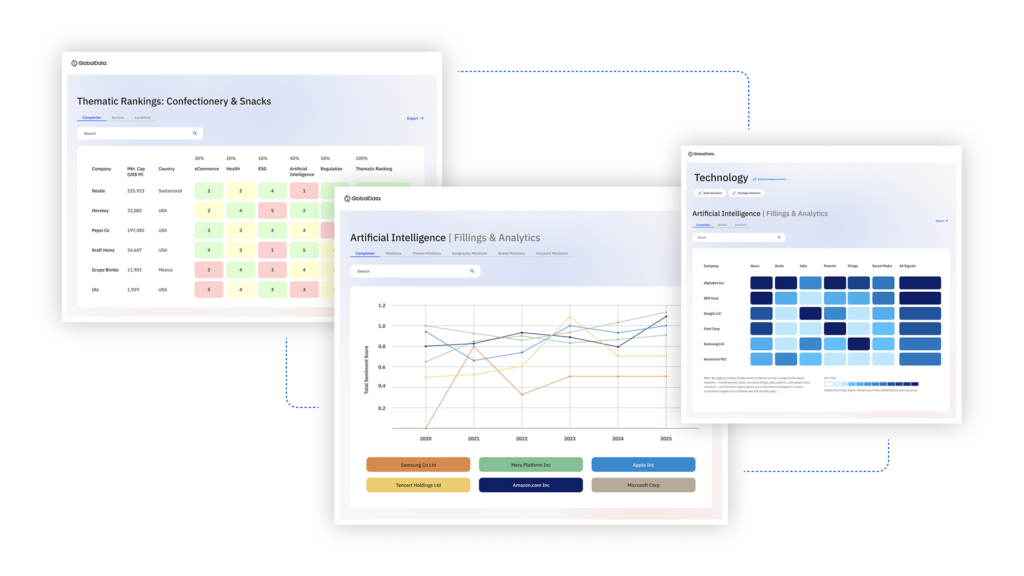
US Tariffs are shifting - will you react or anticipate?
Don’t let policy changes catch you off guard. Stay proactive with real-time data and expert analysis.
By GlobalDataIn order to describe fully the problem, it is necessary to specify the initial temperature distribution within the body and the boundary conditions over the bounding surface of the body. A listing of the thermal boundary conditions commonly employed includes a prescribed surface temperature, a prescribed heat input, a perfectly insulated surface and a convection or radiation boundary condition.
In case of complex boundary conditions or variable thermal properties, numerical solution methods, based on the discretization of the body in a number n of layers, can be adopted to solve the heat transmission equation. According to these approaches, the Fourier’s equation is replaced by a set of n algebraic equations for the unknown temperatures at the n points of the body. Amongst all available numerical methods, the finite difference approach is relevant at this point. The procedure starts with the identification of a layout of points in the space-time domain ℜ, included within the length of the body L and the ending time of the analysis t*. A space and time mesh is established with equidistant space and time mesh sizes h and k. The method consists in replacing the second space derivative and the first time derivative of temperature with simpler differences. In case of temperature-independent material properties within the body, the temperature value at the generic point i and time j+1 can be evaluated once known the temperature values at points i, i+1 and i-1 at time j. It can be demonstrated that the stability condition of the numerical method consists in a coefficient =k¯αk/h2 lower than 0.5.
2. Fire inside a tunnel lining: initial and boundary conditions
With reference to the examined case of fire inside a tunnel lining, the initial temperature distribution within the section is assumed constant and equal to 20 °C. On the extrados side of the transverse section of the tunnel segment, a prescribed surface temperature equal to 20°C is imposed, due to the presence of soil. A combined convection and radiation boundary condition is specified on the fire-exposed surface, according to UNI EN 1991-1-2:2004. The net heat flux h• net is determined by considering heat transfer by convection h•net,c and radiation h• net,r. According to UNI EN 1991-1-2:2004, the coefficient of heat transfer by convection αc, the Stephan Boltzmann constant σ and the emissivity factor ε can be taken equal to 25 W/m2K, 5.67•10-8 W/m2K4 and 0.7, respectively.
Fire scenarios available in codes can be used in tunnels. For example, the following reference is related to two widely spread fire curves, the standard fire ISO 834 and the RWS curve. The first, developed for general buildings and contents, can be also used since its energy content is similar to the one obtained through fire analyses for tunnels and metro tunnels. The latter, typical of railway and road tunnels and developed by the Ministry of Transport in Netherlands, is based on the temperatures expected from a 50m3 fuel, oil or petrol tanker fire in an enclosed area.
The other two vertical sides of the section are assumed to be in adiabatic conditions.
3. Thermal and physical properties of FRC
For FRC typically used in precast tunnel segments, according to CNR DT 204/2006, the thermal properties can be considered to be similar to ordinary concrete. In particular, the curves of thermal conductivity, density and specific heat versus temperature proposed in UNI EN 1992-1-2:2019 can be used. The thermal conductivity λ can be determined between lower and upper limit values.
The variation of the density ρ with temperature, influenced by water loss, can be defined through a multilinear law, defined starting from the value ρ(20°C) of the density of the FRC material at a temperature value equal to 20°C.
For siliceous and calcareous aggregates, the specific heat c of dry FRC concrete (u = 0 %) is given by a multilinear law. For different values of moisture content, the function of the specific heat can be modelled by a constant value cpeak, in the range between 100 °C and 115 °C, and a linear decrease between 115 °C and 200°C. Values of cpeak equal to 1470 and 2020 J/kgK can be adopted for moisture contents of 1,5% and 3.0% of concrete weight, respectively.
4. Temperature-dependent constitutive law of the FRC material
According to FIB Model Code 2010 and FIB Bulletin 83 “Precast tunnel segments in fibre-reinforced concrete”, a rigidplastic model can be used for FRC in both compression and tension, based on the design values of the compressive strength ƒcd and of the post-cracking strength for the ultimate crack opening ƒƒFtud. Partial safety factors equal to 1.0 have to be taken in fire analysis, for both concrete and fibres, due to the exceptional nature of the action.
The degradation of the material properties with rising temperature, with reference to steel fibres, can be modelled similarly to ordinary concrete. For the compressive behaviour, the temperature dependent strength relationships available in codes can be used, as for example the curves proposed in UNI EN 1992-1- 2:2019, which give the trend of the ratio ƒc,θ/ƒck versus temperature, for both cases of siliceous and calcareous aggregates, with ƒc,θ the characteristic compressive strength at temperature θ and ƒck the characteristic compressive strength at 20 °C.
For the tensile branch, it is important to understand the variation of the post-cracking strength for the ultimate crack opening with temperature ƒƒTuk(θ). It is defined as the characteristic residual strength ƒR3k at CMOD=2.5 mm, obtained through a three-points bending test on a notched beam, divided by 3.0. For example, the tensile strength/temperature relationship proposed in CNR DT 204/2006 can be used, based on a temperature dependent coefficient KFt(θ), defined through a multilinear l aw.
5. Residual bearing capacity of FRC sections
For example, the thermal field within the FRC section can be shown by means of either coloured maps, in which colours refer to areas with different temperature values, or temperature/ thickness curves.
The residual bearing capacity of the FRC section after a duration t of the fire event is assessed by means of Bending Moment M versus Axial Force N envelopes. The procedure provides for the subdivision of the section in ns strips with constant height hs, each one comes with a known value of the temperature T, resulting from the thermal analysis previously performed. The M-N envelope is drawn by imposing a vector of neutral axes Χ and writing the two equations expressing the translational and rotational balance of the FRC section. For each position of the neutral axis χ, the stress distribution corresponding to the adopted rigid-plastic model is defined accounting for the material degradation through the aforementioned relationships, being known the temperature of each strip.
The behaviour of the segment is different for sagging or hogging bending moment. It happens when the tensile or compressive stresses are the intrados as in tunnels the fire-exposed surface is the intrados only.
An example of Bending Moment-Axial Force envelope varying the fire curve duration is shown for:
- ISO 834 fire scenario;
- C 40 FRC 4.0 c material;
- 1 m wide, 0.3 m high section;
- a siliceous aggregate concrete.
The upper and lower parts of the domain (sagging and hogging bending moment respectively) refer to the cases of tensile or compressive stresses at the hot edge of the section. As expected, a more marked reduction of the M-N envelope is found in case of hogging bending moment, since, as well known, the structural behaviour is less influenced by a variation of the design tensile strength than a change in the compressive one.
It is worth to highlight the existence of a significant difference in the bearing capacity of RC and FRC sections exposed to fire action. A comparison is shown considering the presence of a sagging bending moment only and the ISO 834 scenario. The amount of steel reinforcement of the RC section, made of a C40 ordinary concrete and having the aforementioned geometry, consists of 4 bars of 12mm diameter each with 20mm concrete cover to ensure an equality with the FRC section, in terms of ultimate bending moment, at temperature equal to 20°C. For the degradation of the yielding strength of the steel reinforcement, the relationships proposed in UNI EN 1992-1-2:2019 can be used. The comparison of the two sections is made in terms of ratio between the ultimate bending moments in presence of fire and at room temperature, at increasing fire duration. For the RC section, an initial time interval is required to reach the concrete cover distance values of quite high temperature to determine a degradation of the mechanical properties of the traditional steel reinforcement. Once this period of time has elapsed, the steel reinforcement undergoes to a rapid decrease of its mechanical properties, with a consequent marked decrease of bearing capacity. Vice versa, in case of FRC sections, the degradation of the mechanical properties starts from the beginning of the fire event. Nevertheless, lower derivatives characterise the reduction in bearing capacity, being the tensile resistance smeared on the entire part of the section subjected to tensile stresses.
6. Numerical survey
A parametric survey, specifically related to geometries and FRC materials used for tunnel segments, allows highlighting the main parameters influencing the residual bearing capacity of the section and identifying the worst or better scenarios. The thermal analyses and the consequent evaluation of the Bending Moment-Axial Force envelopes are performed for:
- ISO 834 and RWS fire scenarios;
- C 50 FRC 4.0c material;
- 1 m wide, 0.3m high section;
- a siliceous aggregate concrete.
Between these two considered fire scenarios, greater temperature values and temperature derivatives are obtained within the FRC section by considering the RWS fire curve.
With reference to the outcomes of the previous thermal analyses, the residual bearing capacity of the FRC section is assessed after two values of fire duration, equal to 30 and 120 minutes . The Bending Moment-Axial Force envelope at room temperature, marked with a continuous line, allows to highlight the degradation of the section at increasing fire duration and the different behaviour for sagging and hogging bending moment. As expected, the M-N envelopes evaluated with the RWS fire curve are entirely contained inside the ones computed with the ISO 834 fire curve, due to the higher values and derivatives observed with the first scenario.
Another useful structural application of the performed analyses consists in finding different combinations of fire scenario and fire duration, giving an equivalence of the FRC section in terms of residual bearing capacity. For example, the RWS fire scenario after 30 minutes produces the same effects of the ISO 834 fire scenario following 60 minutes. Similarly, it stands for the RWS fire curve imposed for a duration equal to 60 minutes, which causes the same degradation in terms of residual bearing capacity given by the ISO 834 fire curve after 120 minutes.
To express the degradation of the FRC section in term of loss of thickness, the proposed procedure can be used to perform a parametric survey, by keeping fixed fire scenario and FRC mechanical properties, but varying the height of the section and the fire duration. For example, considering the RWS fire scenario, the residual bearing capacity of a 0.35m high section after a fire duration of 120 minutes is equal to the one of either a 0.3m high section after 30 minutes or a 0.25m high section at room temperature.
Conclusions
The structural behaviour of FRC sections, without any traditional steel reinforcement and exposed to fire action, can be assessed through Bending Moment–Axial Force envelopes accounting for the constitutive relationships of the FRC material varying temperature. The analytical procedure set out, specifically related to precast segments for mechanically excavated tunnel linings, represents a useful tool for both design phase of structures exposed to fire and rehabilitation after a damage occurred during an exceptional event.
One of the most beneficial effects of the presence of fibres within the concrete matrix, it is the less appreciable degradation of the tensile mechanical properties, which results in a smoother degradation of the bearing capacity of the FRC section with respect to RC section.
For tunnel segments, a different behaviour is found for sagging and hogging bending moment, since the fire exposure is in the intrados region only. In particular, a higher decay of bearing capacity is found for hogging bending moment, such as compression at the intrados.