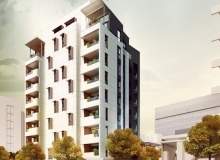
Thriving urban city centres are not where you would usually expect to find large wooden structures dominating the sky line, but rather glass, steel, brick or concrete formations. However, due to its sustainability and CO2 consuming properties, timber is fast becoming the construction material of choice for architects tasked with building housing blocks, schools and libraries in inner cities.
After being largely unused in modern cities in the UK for centuries, why are architects now returning to wood – a raw organic material that was once actively avoided as a construction material due its tendency to thrive in an errant fire?
Timber’s new renaissance and green credentials
The Great Fire of London in 1666, which saw a third of London’s largely wooden buildings destroyed, heralded a new era of building regulations where construction with wood would be forbidden. That is until 1999, when a new safety test carried out by the BRE (Building Research Establishment) on a six-story timber framed building concluded that the fire was successfully contained.
This led to the relaxation of the use of timber in modern day construction. Since then the use of timber, mostly timber framed buildings, in the UK has gradually boomed. In the last few years this boom has intensified with architects creating large scale urban buildings made almost entirely of Cross Laminated Timber (CLT). This is a type of reinforced timber made up of several large sheets of timber glued together for increased rigidity and strength. CLT has been certified for a minimum 60 year lifespan by the BRE.
According to David Hopkins from the Timber Trade Federation, timber’s new renaissance is being driven predominately by the UK’s current environmental agenda. Timber is an environmentally-friendly material because it absorbs CO2 instead of omitting it, and then releases oxygen back into the air. Unlike concrete and brick; concrete uses five times, and steel six times, more energy to produce than timber.
A report by CEI-Bois, the European Confederation of woodworking industries, entitled ‘Tackle Climate Change: Use Wood’ published and revised in 2011 stated that: "A 10% increase in the percentage of wooden houses in Europe would produce sufficient CO2 savings to account for about 25% of the reductions prescribed by the Kyoto Protocol."
Timber also helps insulate buildings, helping contain energy throughout its lifetime. According to the report, timber does this: "15 times better than concrete, 400 times better than steel and 1, 770 times better than aluminum." It is also a recyclable material that can be reused.
Timber’s convenience, affordability, lightweight properties and the fact it lends itself to offsite construction are also other major pulls for architects, especially when working in busy cities on affordable housing projects.
Andrew Waugh of Waugh Thistleton, the architects responsible for Stadthaus in Hackney, London, a nine-storey timber building, explains why they chose to use timber: "You don’t need to construct a tower crane to assemble the building because it is a quarter of the weight of a concrete building – everything can be done from the back of a lorry. It is very quick."
"It’s very quiet, because there is no cement mixers or jack hammers, it has excellent acoustic properties, so good for an urban environment; it keeps outside noise outside."
Timber buildings such as Stadthaus, which is made from CLT, are not built onsite as concrete or brick building would be, but rather created offsite and assembled onsite, which is a much quicker construction process.
Timber as a building material: what’s the downside?
Timber-skeptics have pointed out the downsides of timber. In 2010, a BBC investigation questioned the credibility of the original 1999 BRE safety test on the six-storey timber framed building, stating that the report failed to note that the fire, hours after the test, reignited in the middle of the night.
This, and incidences such as the Carisbrooke Gardens housing estate fire in Peckham in 2009, where 300 people were forced to flee their homes after the estate went up in flames after a fire at a nearby construction site of 39 timber framed homes, prompted concern and a report by The London Assembly. However, while fire safety and how quickly it spreads in timber framed housing is considered questionable, Waugh says CLT buildings do not hold the same risks.
"You are talking about massive bits of timber, so actually the surface area and mass of the material is that much greater. Timber is incredibly predictable in a fire so in many ways a solid timber building performs more predictably in a fire than the equivalent concrete buildings."
Timber also helps insulate buildings, helping contain energy throughout its lifetime
Hopkins agrees, saying: "This is the reason that fire doors are made of wood, not metal or concrete!"
Timber-skeptics also point out that although timber stores carbon it uses a lot of CO2 to transport it around Europe; it is currently predominantly produced in Scandinavia and Austria.
For example, the transport impact of the panels transferred from Austria for Bridport House was calculated as 45 tonnes of CO2. However, Hopkins dismisses that this as an issue and says: "A recent peer reviewed study by the American Hardwood Export Council showed that the amount of carbon absorbed by the tree as it grows far outweighs all of the emissions produced during harvesting, processing and transportation across the Atlantic to the UK."
Many consider wood to be less durable, falling foul to damp and rot. Can wooden buildings really be made to last as long as concrete and brick? To this Waugh’s reply is simply: "There’s a [wooden] church in Essex that was completed in the sixth century and it doesn’t get concrete cancer and it doesn’t rust."
He also points out that CLT constructed buildings are kiln dried to avoid rotting, but even if they still rotted it could be cut out and replaced.
Modern timber developments
Bridport House in Hackney, London
Part of the Colville Estate regeneration project by Hackney Council, Karakusevic Carson Architects were appointed to provide 41 socially affordable homes.
Paul Karakusevic of Karakusevic Carson explains why they used timber for the building: "We wanted to make the building as sustainable as possible and the timber helped to reduce the overall carbon footprint.
"The site is located directly above a major storm water sewer, so we had to make the new structure as light as possible to reduce the time needed for negotiations with Thames Water."
The building is made of CLT, which they also covered in plaster board to help with acoustics, and is covered with bricks on the outside. It took just 27 days and three people to build. The wood was sourced from Stoa-Rensa, Austria.
It’s the fourth time Karakusevic Carson has used CLT and it also has three more major projects in the pipeline, comprising of more than 1,000 homes.
Forté in Victoria Harbour, Melbourne
The world’s tallest residential timber building made from CLT was developed by Lend Lease. Forté, which will be completed this month, is the first building in Australia to made of CLT.
Forte offers 23 boutique apartments, ranging in price from $430,000 to $795,000, spread out over a ten-storey 32 metre high building.
Lend lease believe by using timber as the main construction material for Forté they saved 30% on the construction time and that residents will save around AUS$300 on bills due to its excellent insulation properties.
A spokesperson from Lend Lease also stated that: "By using CLT, the project will reduce CO2 equivalent emissions by more than 1,400 tonnes when compared to concrete and steel – the equivalent of removing 345 cars from our roads."
The success of Forté, the first of its kind in Australia, could see more timber buildings being built there.
The spokesperson added: "The company is assessing a number of projects to see the potential to develop 30-50% of its apartment pipeline using CLT along with application elsewhere across the Lend Lease Group. CLT will assist to address two key growth trends that Lend Lease has identified in its strategy – sustainability and urban regeneration."
Stadthaus Residential Development in Hackney, London
When built in 2009 Stadthaus was the tallest timber building in the world, comprising of 29 apartments over nine storeys. It has since been overtaken by Forté Living.
Its ground floor is made of concrete in order: "To take the timber of the ground and make sure any failures in the damp-proof membrane didn’t interrupt the structure," says Waugh.
The building was commissioned by Metropolitan Housing Trust and developed by housebuilder Telford Homes. The wood was sourced from Europe and Scandinavia.
Waugh says he believes timber is the future: "It will be the principle building material within a decade because concrete is a massive polluter and it’s not very nice to live in or build with."
Waugh and Thistleton have just erected a mixed use CLT building in Shoreditch.
Related content
Old as the hills: traditional building materials in the 21st century
Materials such as straw, clay and rammed earth have been pushed out of the mainstream by 21st century concrete and steel, but these materials are still a viable option for eco-conscious builds.
Nature’s bounty: biomimetics in design and construction
Could nature become as big an inspiration for construction materials and design techniques as it has been in other fields?