
Prefabricated housing has an image problem. Despite decades of advancements in the field and the many impressive projects that have been carried out over the years, there has been a general perception that prefab houses are an ugly throwback from post-war emergency house-building projects such as the UK Ministry of Works’ Emergency Factory Made housing programme in the late 1940s, which introduced the ‘Airey houses’, with many still standing today.
Modern prefab houses have introduced a wider range of materials and aesthetic concepts that can be applied in a short space of time. Manufacturers such as Germany’s Huf Haus have evolved the prefab building concept to incorporate appealing wood and glass components, and achieve high standards in sustainability and energy efficiency.
Despite the post-war recovery years now being a distant memory, housing shortages, and especially of affordable family homes, are still an everyday concern for local governments around the world. As prefabricated houses continue to improve, they are increasingly being considered as a fast but high-quality solution to local housing crises. In August 2013, Bristol City Council was touting prefab as a recommended option to house the 14,000 people on the city’s waiting list.
In July 2013, Slovenian wooden prefab house manufacturer Riko launched the latest iteration of its eco-friendly, modular prefabricated housing concept, developed in partnership with famed French designer Philippe Starck. Known as P.A.T.H. (Prefabricated Accessible Technological Homes), the range combines modern standards of comfort and technology with energy efficient features, a flexible layout and a manufacturing time of just six months.
We caught up with Riko’s project coordinator for P.A.T.H. Katarina Kumelj to discuss the benefits of the P.A.T.H. range, Starck’s influence on the project and the changing image of prefab houses.
How well do you really know your competitors?
Access the most comprehensive Company Profiles on the market, powered by GlobalData. Save hours of research. Gain competitive edge.
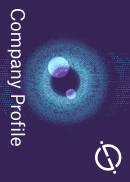
Thank you!
Your download email will arrive shortly
Not ready to buy yet? Download a free sample
We are confident about the unique quality of our Company Profiles. However, we want you to make the most beneficial decision for your business, so we offer a free sample that you can download by submitting the below form
By GlobalDataChris Lo: Could you give some background on Riko’s previous work in prefabricated wooden buildings?
Katarina Kumelj: One of Riko’s key focuses is sustainable and low-energy wood construction, since 1997, Riko has been manufacturing and building tailor-made ecological and energy saving wooden constructions, prefabricated in our production facilities in Slovenia based on our own patent.
By applying state-of-the-art technology and a know-how inspired by our centuries-long local tradition of wood crafting, Riko has developed into an internationally recognised company, having carried out numerous private and public projects across Europe, in Italy, the UK, France, Germany, Sweden and Switzerland, among others.
Our commitment to the tailor-made approach has made it possible for us to carry out numerous one-of-a-kind wooden prefabricated projects in the likes of individual and multi-residential projects, as well as various public buildings, such as kindergartens, schools, congress centres, wellness centres and hospitality buildings.
CL: When did you decide to pursue the P.A.T.H. project with Philippe Starck, and what research and development went into the project before the launch in July 2013?
KK: Philippe Starck is the founder of the concept of Democratic Design. He strives to increase the quality of the products while making them accessible to the greatest number of people. Following this premise, he developed the concepts of Democratic Ecology and Democratic Architecture.
Philippe Starck has since been looking for a partner to help him realise his vision of Democratic Architecture, a collection of houses, which would feature the best plans and would be built with the help of the best technological construction, granting quality of design and quality of manufacturing.
2009 marks the beginning of the official collaboration between Starck and Riko, in which Philippe Starck’s creativity, vision and conceptual design have been merged with Riko’s engineering and production knowledge, as well as industrial and production capability.
In our joint research and development, we strived to create a reliable and intelligent living solution for today’s generation and generations to come. When developing P.A.T.H., we focused on the following key issues: inventing an intelligent and timeless design that would provide maximum comfort of living for its users; selecting high-quality and sustainable construction materials; the use of efficient production and building processes; and finally, the integration of renewable energy sources and a top-of-the range turn-key that would result in an energy-efficient and comfortable day-to-day life.
CL: How has Philippe Starck’s design style influenced the development of P.A.T.H.?
KK: Philippe Starck defends the notion of creating a style that will still be acceptable and appreciated in 50, 100 or even 200 years. It was much more than style that influenced the development of the concept, rather it was Starck’s vision and imagination of what a new route, a new way of apprehending individual housing should be. That meant inventing a turnkey living solution, which would be built with the right materials, offered at the right price, made in irreproachable quality and produced with the best process that technology has to offer.
CL: How successful has P.A.T.H. been with European customers since the launch? Are you considering launching the range in other regions as well?
KK: P.A.T.H. has received a lot of positive feedback and has raised interest from customers and media worldwide, not only in Europe. We have had requests coming in from the US, Central and South America, Asia and Australia. While we are currently focused on European distribution, we are considering expanding the P.A.T.H. network of distributors to other regions as well, especially to the US.
CL: How does P.A.T.H. expand Riko’s previous work on sustainability and eco-friendly living, and how does technology help to achieve this?
KK: P.A.T.H. is the result of Riko’s embedded imperatives: innovation, dedication to details and to the highest ecological standards, while it has been expanded to a larger-volume, more industrial scale. Prefabrication technology has played a crucial role in the amplification of the P.A.T.H. line of houses as it allows for consistency in quality throughout the manufacturing and construction process, it yields substantial overall time-savings, it drives down the production and construction costs and it guarantees steady performance of the building throughout its use.
CL: Can P.A.T.H. houses be purchased affordably, with savings on energy and other living costs?
KK: The main advantage of prefabricated building is that the time savings, enabled by a closely monitored all-year-round factory production, result in a decrease in production and mainly construction costs. We leave little to no room for error, which is highly beneficial.
As for energy savings, we are aware that the use of renewable energy technology is first and foremost an investment into the future.
Opting for state-of-the-art technological equipment, such as photovoltaics, solar panels, heat pumps, wind mills and rainwater collectors that can be combined and integrated into the P.A.T.H., means savings on energy and other living costs in the long run.
CL: How are you able to achieve a turnaround time of six months to build the houses?
KK: Once a particular P.A.T.H. house has been chosen, then follows the project making and production process. Using prefabrication, every detail of the P.A.T.H. home is subject to careful planning and engineering already in the initial phase, which minimises any chance of error later on.
Each large building component of the P.A.T.H., such as external and internal walls, is then prefabricated in Riko’s closed, dry and rigorously controlled production facility. There, the elements are protected against the effects of weather and can be manufactured all year round, even in the wintertime. All building components are pre-manufactured to the highest degree, including the exterior façade and frame, are filled with insulation and finished with closing panels.
This level of prefabrication reduces the duration of the on-site assembly process considerably compared with traditional on-site building techniques. After the initial infrastructure has been made and the foundations laid, the assembly of the house structure only takes several weeks, after which the roofing follows.
After the P.A.T.H.’s structure has been erected, approximately two more months are required to finalise the electrical and mechanical installations and to equip the P.A.T.H. with all the finishes and fit-outs a client had selected at the beginning of the decision-making process.
CL: When manufacturing the homes, how flexible can you be to customers’ individual specifications?
KK: There are plenty of ways to adapt a P.A.T.H. home to an individual needs and specifications. Firstly, the diversity of the P.A.T.H. models in terms of the floor plans, structure systems, roof types and fit outs already covers a wide variety of location-based and regulatory constraints and can in this way answer to the individual needs of customers.
Further flexibility is enabled through the concept of P.A.T.H.’s intelligent, functional and large, open plans that merge living room, kitchen and dining area into a single, completely open space without imposing any predetermined delimitation of space in the form of walls or pillars. This approach permits for personalised rearrangement of the interior layout, furniture and equipment, however the client chooses it.
And finally, when it comes to the interior finishes, Philippe Starck has handpicked a selection of top-range designer exterior and interior equipment and finishing options, gathered in the catalogue of P.A.T.H. fit-outs and finishes.
This way customers can choose from a multiple and varied choice of different roof types, facades, interior finishes and fixtures, such as flooring option, ceramic tiles, bathroom equipment, lights, switches, as well as eco-technology packages, etc. The customers can mix-and-match the options and create their own compelling living space.
CL: Which design features of the P.A.T.H. range do customers get most excited about?
KK: Admirers of wooden construction are most impressed by the interior spaces, which are divided by solid wooden partition walls and closed with solid wooden ceiling panels, made of visible spruce wood which is finely brushed to enhance the natural texture of the wood.
Another feature which gets a really positive response from the customers is the floor-to-ceiling glass façade encased in thin 130mm powder-coated aluminium, which gives P.A.T.H. an elegant appearance. These large glass surfaces seamlessly merge the interior with the surroundings, allowing the interior to bask in natural light.
Customers are also impressed by the signature curved cornice roof, a remarkable structure that crowns the house. It is made from the same high-tech light and durable material that is used in building boats and yachts, fibreglass.
The large arches of the cornice roof provide shelter and additional shade to the rooms below. In addition, the hollow ‘sinks’ of the cornice can act as flowerpots that are able to host lush greenery that spills over the corners of the roof and seamlessly blends P.A.T.H. with its surroundings. The plants in the flowerpots can be watered with the help of a rainwater collector system, which is a great feature for eco-aware customers.
CL: Do you think prefabricated homes could offer the best solution to the housing shortages being experienced in many countries?
KK: For too long, construction has been placing an increased burden on to the social and natural environment, especially through the growing issues of resource and energy consumption, greenhouse emissions and waste generation, among others. In the face of these questions, wooden prefabrication is indeed the optimal answer, because it represents a truly sustainable, fast, flexible and cost-efficient building production technique.
CL: Do you think there is still a perception that prefabricated buildings are ugly post-war structures? Is P.A.T.H. a reaction to that stereotype?
KK: Although this might have indeed been the general notion even a decade ago, I have seen that in the past couple of years prefabrication, especially wooded prefabrication, is experiencing a true renaissance. It is finally starting to get the recognition it deserves.
P.A.T.H. is in part a reaction to the stereotype, but mostly it is a result of Starck and Riko’s desire to create a unique living solution that is done in a better and fairer way. A solution that is intelligently and responsibly designed, engineered and produced in such a way that it reduces its impact on the environment and natural resources, and withstands the test of time.
Related content
Vertical village: the future of high-rise living
The vertical village concept offers a vibrant alternative to drab and dreary residential tower blocks.
Welcome to the library of the future
The newly-opened Library of Birmingham could point the way to a 21st century library that can survive and thrive in the digital age.