Brought to you by
Although many other tunnelling methods have been developed in last 200 years, drill-and-blast is still the conventional method for noncircular cross-sections. Circular tunnels too short to amortise the high start-up costs of a TBM or too hard to justify the cost of cutter replacement for smaller machines such as roadheaders also use this technique.
The typical cycle of excavation by blasting is performed in the following steps: drilling blast holes and loading with explosives > detonating the blast, followed by ventilation to remove blast fumes > removal of the blasted rock (mucking) > scaling crown and walls to remove loosened pieces of rock > installing initial ground support > advancing rail, ventilation, and utilities.
The explosive is generally a chemical compound or mixture ignited by heat, impact, friction or a combination of all three. Upon ignition, it decomposes very rapidly in a detonation (as opposed to a deflagration, which is slower and occurs for instance with gunpowder). Upon detonation, heat (~4,500°C) and large quantities of high-pressure gases (~250,000 bar) are released. The gases expand at high force to overcome the confining forces of the surrounding rock formation. Common types of explosives include: dynamite gelatins, ANFO, slurries, and emulsion.
Many factors must be considered in the design of a blasting round. Controlling surface effects is essential in urban areas. This is accomplished by specifying limits on the pounds of explosive per delay, the sound increase in decibels, the maximum particle velocity at adjacent building foundations, and the permissible air overpressures.
Two parameters are often calculated from a blast design: the “powder factor” or specific charge, i.e., kilogram of explosives per cubic metre of blasted rock, and the drill factor, i.e., total length of drill holes per volume of blasted rock m/m3. These are indicators of the overall economy of blasting and permit easy comparison among blast patterns.
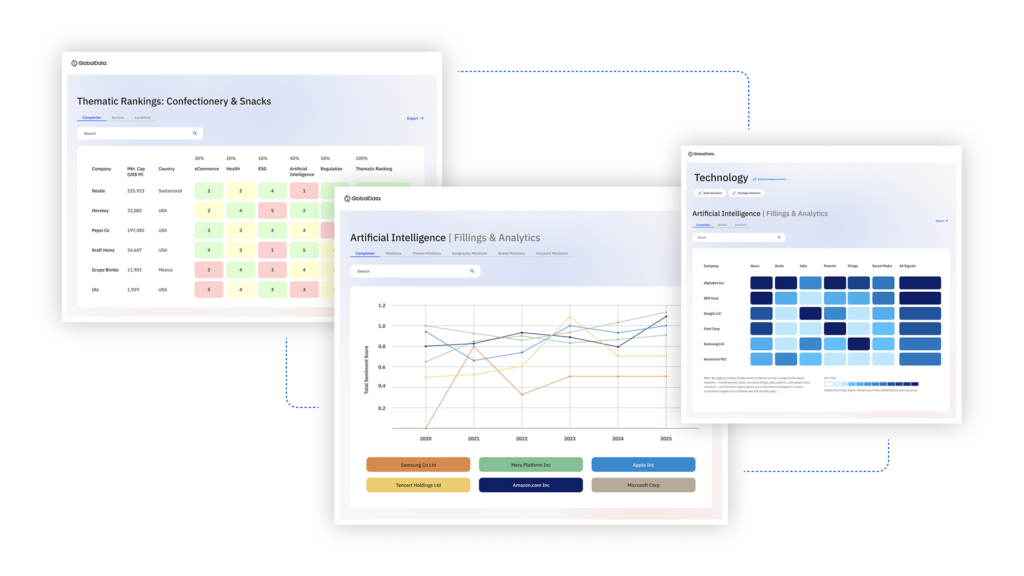
US Tariffs are shifting - will you react or anticipate?
Don’t let policy changes catch you off guard. Stay proactive with real-time data and expert analysis.
By GlobalDataThe correct blast pattern design ensures the distribution of the explosive in the rock and desired result. The blast designer’s main concerns are that the quality of the host rock and the shape of the tunnel, especially the arch, be maintained. Controlled blasting requires closer spacing of the profile (perimeter) holes plus reduced charges in these holes. Among the construction concerns for the blast engineer in a firing sequence (delay pattern) is providing efficient breakage and muck pile concentration, proper rock fragmentation to facilitate mucking operations, drillhole diameter, spacing, and burden (measured parallel and perpendicular, respectively, to the momentary free face) and lastly, explosive strengths.
One of the standard methods used in controlled blasting is smooth blasting. Here, a line of holes are drilled along the walls and arch at closer spacing than the production holes, loaded with slightly lower-strength and well-distributed charges, and shot on the last delay or two in the production round.
Amount of explosives: experienced blasters forecast the amount and number of explosives required and optimise it as they observe the operation. The powder factor will vary from about 2Ib/yd3 (1.2kg/m3) for a large opening, i.e., more than 1,000sqf (93m2) in the soft fractured rock, to more than 9Ib/ yd3 (5.3kg/m3) for a 100sqf drift in hard intact rock.
A reliable way to determine blast vibrations (particularly around residential or sensitive industrial areas) is to install and monitor a seismograph to verify the severity of vibrations. This will permit field adjustment of loads per delay to the maximum output consistent with negligible damage
Overbreak is the unintended excavation that happens outside of the designed excavation line of a tunnel due to the irregular pattern of rock breakage, which often can be unavoidable after the blast. However, it can be minimised by using controlled blasting. The definition also relates to the concrete required to fill this over-excavated space in lined tunnels.
As a tunnel or excavation progresses, the roof and side walls need to be supported to stop rock from falling into the excavation. The philosophy and methods for rock support vary widely but typical rock support systems can include: rock bolts or dowels, shotcrete, ribs or mining arches and lagging, cable bolts, and in-situ concrete.