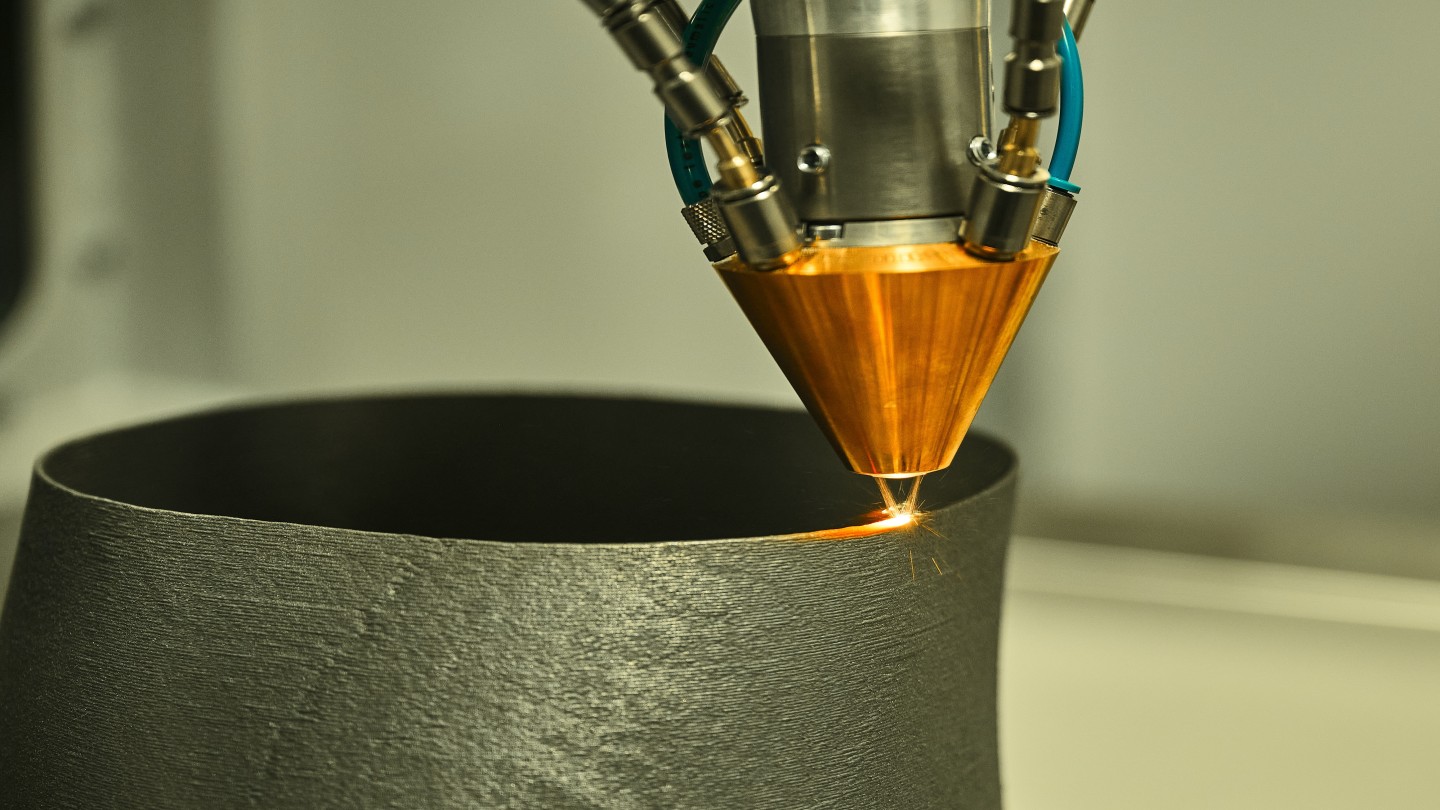
Property development company Litehaus is set to use 3D printing technology to construct a house in Torres Vedras, Portugal.
Located close to the country’s capital, Lisbon, this project aims to address the construction sector’s carbon footprint, which is noted to account for 42% of global emissions.
The primary focus of 3D printing is on walls and involves using technologies such as AI for the initial creative and design phase and 3D printing itself for the construction phase.
Litehaus chief creative officer Simi Launay said: “We are here to distrust the sector. This technology allows us to produce as much as 45m² of walls in only 20 hours.”
The company invests in modular housing and 3D-printed homes, reportedly reducing energy consumption by 67% when compared to traditional manufacturing methods.
It says it integrates technology and sustainability in premium properties, seeking to develop energy-efficient units with lower running costs.
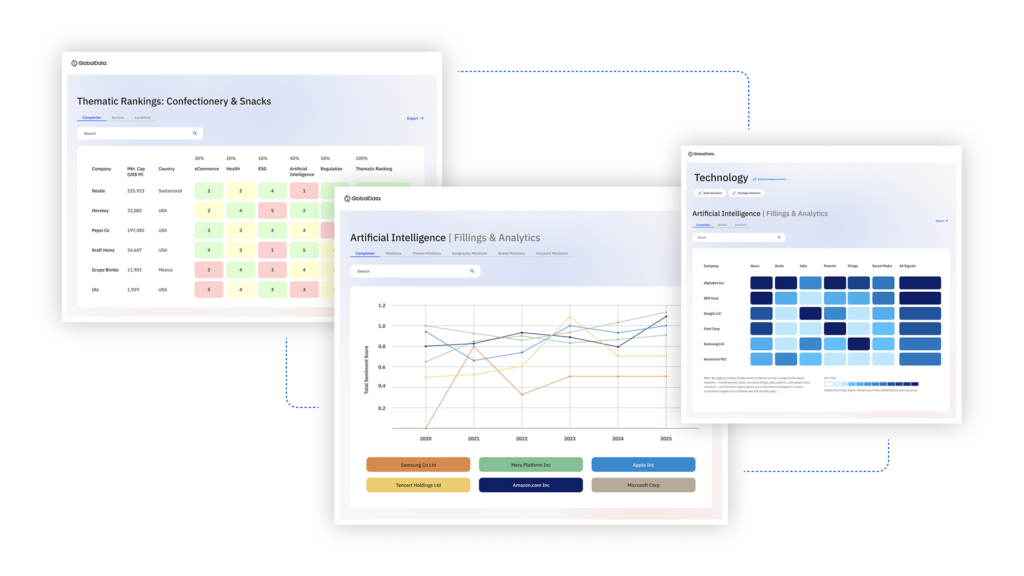
US Tariffs are shifting - will you react or anticipate?
Don’t let policy changes catch you off guard. Stay proactive with real-time data and expert analysis.
By GlobalDataLaunay added: “Litehaus is embarking on a mission to redefine living spaces, fusing AI technology, 3D printing and modular homes to create buildings that resonate with simplicity, innovation and sustainability.
“Our goal is to build 70% faster and 20% cheaper, delivering residences that epitomise elegance and minimalism harmonised with Portugal’s natural beauty.”
In addition, the company plans to construct a complex of 13 3D-printed houses in Torres Vedras, marking the first of its kind in Portugal.
The company aims to build 100 residences annually across the country.