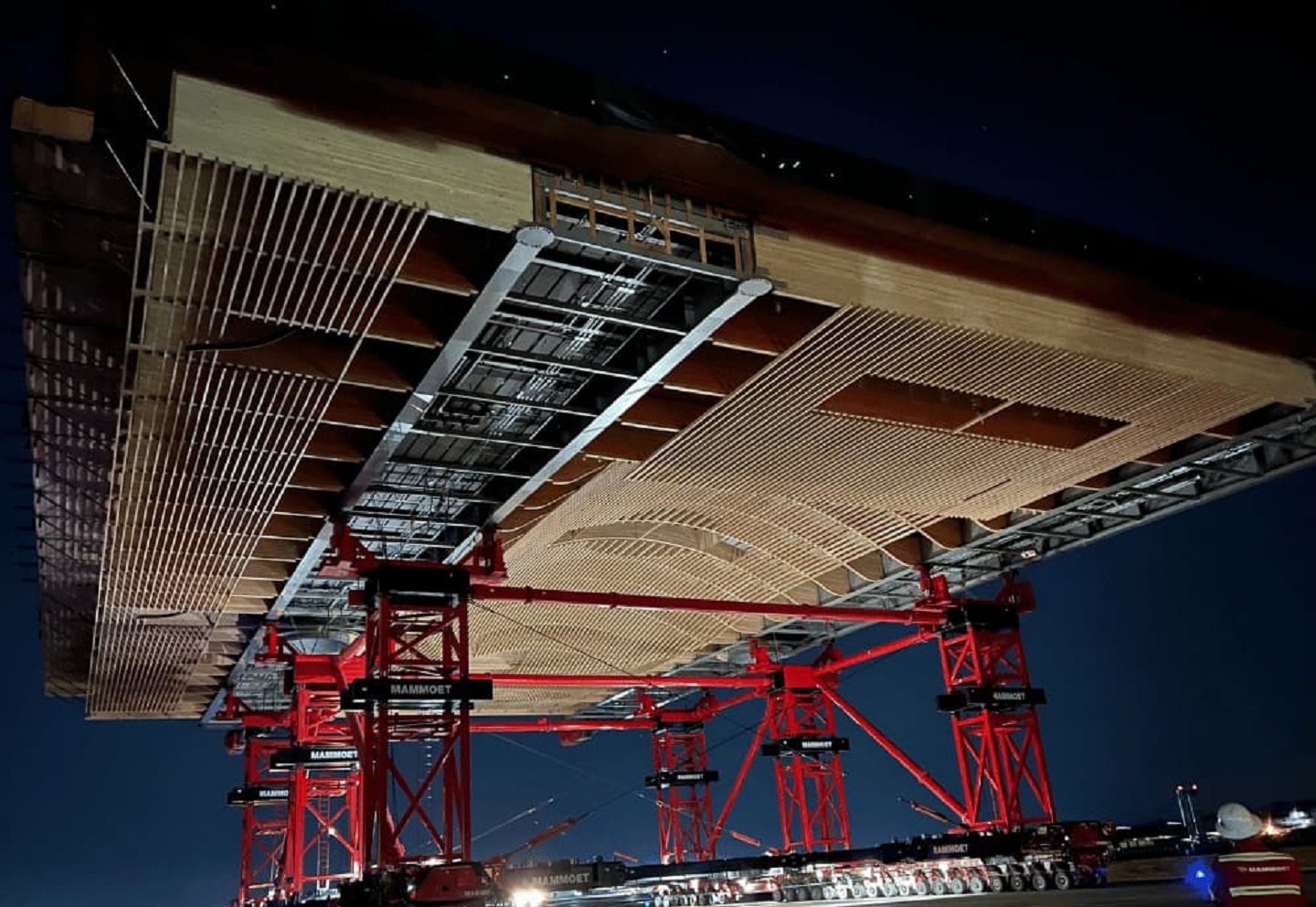
Dutch engineering service provider Mammoet has secured an ongoing contract to jack up, transport, and install 20 panels of five different types for a new roof structure over the central space of Portland International Airport in Oregon, US.
This ‘seismically isolated’ roof structure is a major element of the airport’s main terminal expansion project.
So far, over the course of a year, the roof, which was made primarily of regionally and ecologically produced wood, was completely prefabricated between the airport’s operational runways.
The roof panels were then disconnected into almost football-field-sized sections before being delivered to the new terminal extension.
This is said to minimise disturbance to airport operations. Depending on the panel type, it was either launched, rolled into place, placed directly with self-propelled modular transporters (SPMTs), or lifted using a crane into its final setting.
The panels range in weight from 40t to 632t and have dimensions of up to 72m x 50m x 6m.
Mammoet utilised four Mega Jack 800 towers to jack up the roof panels to roughly 17m to drive SPMTs with falsework below each roof segment.
The majority of the panels had to be erected on top of occupied parts of the former terminal building.
The next batch of panels were then rolled into place along the bottom flanges of the previously set panels.
Before the public could reoccupy the area below, the panels were secured for potential high-wind and project-related seismic requirements.
The deflection of the roof was monitored and kept within set parameters at every point during the jacking, transport, and deployment processes.
Ahead of the execution, Mammoet conducted friction testing in its Rosharon, Texas yard to check if the design values showcased to the customer for strand jack anchoring were ‘realistic’.
Mammoet monitored the loads and deflections on site to verify they were consistent with the tested values.
To date, Mammoet has successfully placed 16 panels to conclude phase one of the project.
Phase two will involve the implementation of four new panels in 2024, once the inside of the terminal expansion has been built out by the client for general occupancy.