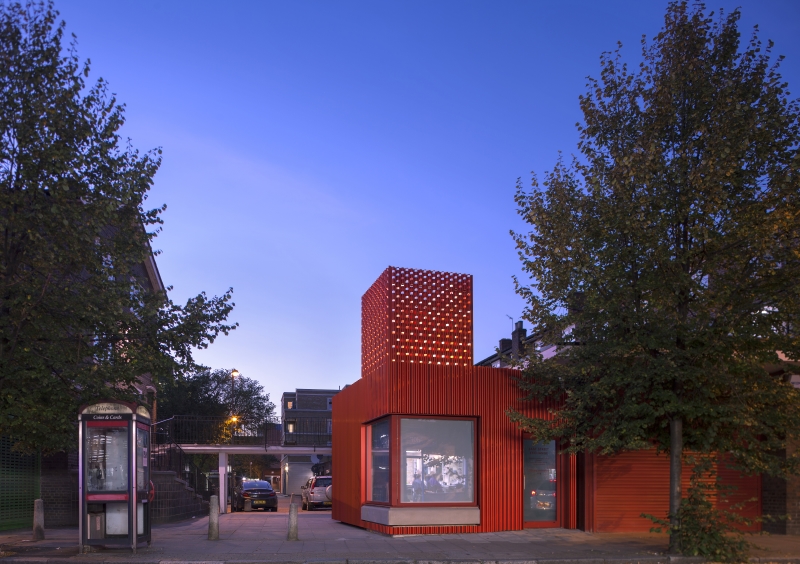
Aluminium Construction: Advantages and Applications
As advances in smelting methods drastically improved the production process for aluminium after the late industrial era, its price plummeted from around $14,000 per metric ton in 1900 to $2,340 by 1948. The newfound accessibility of this lightweight wonder-metal saw it quickly rise to prominence in 20th century architecture and construction, and its appeal hasn’t diminished since then. Today, aluminium is the second most-used metal in construction after steel, with its high strength-to-weight ratio, ductility, recyclability and resistance to corrosion putting it in high demand in both industrial and commercial building.
Common uses of aluminium in the modern construction industry include long-span roof systems, taking advantage of the metal’s high ductility to create consistent and durable forms over wide areas. Aluminium’s inherent reflectivity of heat and light make it an excellent component of exterior facades and cladding systems, while aluminium alloys have the strength to support heavy glass spans while facilitating new and exciting shapes, giving rise to many of the tallest and most innovative skyscrapers now populating the skylines of the world’s premier cities.
With aluminium claiming a firm place near the centre of modern design and construction, below are some prominent examples of the traits underpinning the metal’s appeal, and the innovative techniques that it makes possible.
The green metal
Aluminium’s eco-credentials are increasingly sought-after as 21st century green building standards continue to develop. At the forefront of the metal’s environmental appeal is its endless recyclability; unlike many metals, aluminium and its alloys can be melted down and reused without any compromise on their mechanical properties.
The estimated level of recycled aluminium in components used in building projects is 50-85%, according to US industry group the Aluminum Association, incentivised by the lower costs (in both energy and cash) of using recycled aluminium when compared to freshly-produced metal while a 2004 Delft University of Technology study found that 95% of the aluminium used in new builds is recycled at the end of buildings’ life cycle. Other environmental benefits include energy savings from the use of heat-reflective aluminium roofs, particularly in large tower projects.
As such, aluminium can play an important role in getting new buildings certified by international green building standards such as LEED and BREEAM, as demonstrated this year by ACDF Architecture and Architecture49’s mixed-use Parq Vancouver project in central Vancouver, which employed aluminium louvers along its massive reflective glass façade to maximise natural light. A subtle application, but it still played an important role in securing the project’s LEED Gold status.
Aluminium foam gives new texture to facades
Exterior facades, panelling and cladding represent one of the most common uses of aluminium in construction, with the metal’s flexibility able to easily conform to required shapes while maintaining a strong resistance to corrosion and fire.
Although aluminium composite material (ACM) cladding is currently at the centre of immense controversy due to its exacerbating role in the tragic Grenfell tower fire in June 2017, and the subsequent concerns over the safety of similarly-designed housing blocks, the risks presented by ACM cladding don’t rest with any particular property of aluminium itself, rather the tendency of certain cladding systems to expose core materials such as polyethylene and polyurethane, which are highly flammable if not treated with flame retardants.
An example of a more innovative application of aluminium in building facades is aluminium foam. This material is made by injecting air into molten aluminium, creating air bubbles that can be customised in size, creating texture and allowing variable levels of light to enter or leave a building through its porous surface. The technique was used to startling effect on Spacesmith and Davis Brody Bond’s redesign of the Earthcam headquarters building in New Jersey, which employed aluminium foam to allow light from the building’s interior to softly illuminate the surrounding gardens.
Powerful shapes and contrasts
Aluminium’s ductility allows it to be pulled into all sorts of dynamic shapes and contrasting designs. In London, design studio We Made That achieved a great effect with a limited budget on a project to extend the East Street Library in Walworth.
The extension, dubbed the East Street Exchange, provides two new multi-purpose community meeting rooms, with a corrugated aluminium exterior contrasting against the traditional brick of the main building. The team used chemically anodised aluminium to allow for an arresting red colour, which is matched by interior fittings and picture window frames.
Aluminium’s lightness and flexibility can also support some impressive experiments in twisting form, as suggested by the name of Danish studio Bjarke Ingels Group’s first project in Norway, The Twist. The project is a distinctive art gallery within Kistefos Sculpture Park in Jevnaker, taking the form of a bridge over the Randselva river, which runs through the park. The bridge is made up of straight 40cm-wide aluminium panels laid out in a twisting, accordion-like geometry that gives the gallery a flowing motion over the river as visitors move towards the gallery space, accompanied by views of the river below.
Modular construction
Modular construction involves the remote prefabrication of building elements for reassembly on site, and is increasingly valued for its innovations in manufacturing and the speed with which structures can be built when compared to traditional site-built projects. It’s a rapidly maturing system that can be particularly useful for temporary or semi-permanent structures, and lightweight, recyclable aluminium makes for a smart choice as a primary building material.
World Building Solution has unveiled a rapidly-deployable military hospital structure, the aluminium components of which can be flown to virtually any destination by air and quickly snapped together to offer a massive upgrade to tents and a closer experience to a traditional hospital for injured soldiers or civilians caught up in humanitarian crises.
MOS Studio, meanwhile, saw success at the first Architecture and Landscape Biennal in Versailles, France this year with a modular-built educational space – the ‘Petit Ecole’. The structure was built as a multi-functional children’s workshop, lab and classroom, and is composed of 825 individual aluminium components. While the space’s current spot at Versailles has been extended well beyond the dates of the biennal this summer, it is designed to be speedily disassembled and put back together at any location.